AnyDesk Storage Organizer
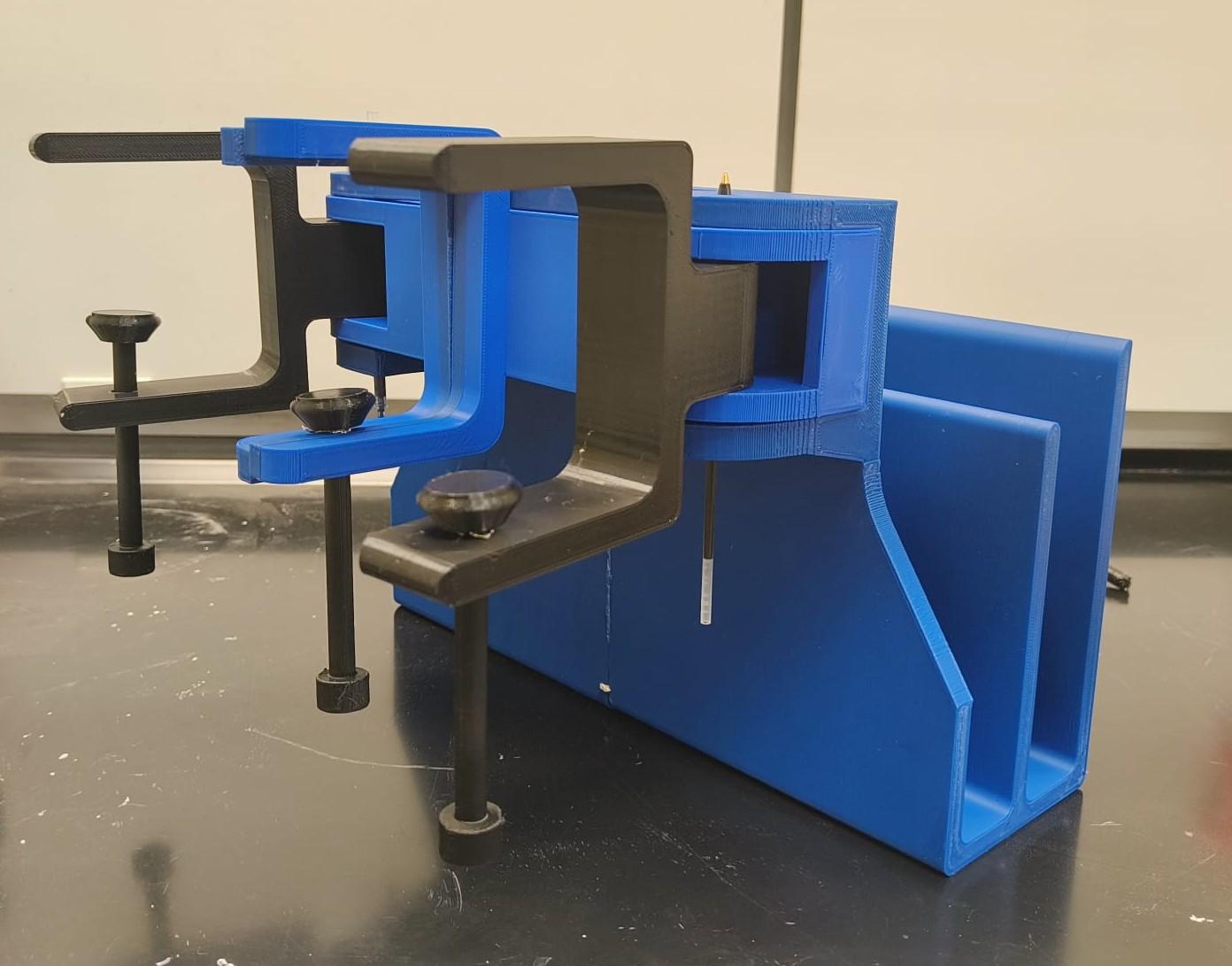
This project presents a modular "AnyDesk Storage Organizer" designed for diverse desk shapes (circular, L-shaped, rectangular), targeting remote workers, students, and office users. Using a combination of CAD, FEA simulation, and 3D printing, we created a workspace solution that eliminates desk clutter, protects electronics, and adapts ergonomically to user needs.
Prototyped in PLA, the final version was optimized for Aluminum 6061-T4, reducing the weight from 3.2 kg to 1.25 kg and increasing durability. The project integrates engineering design, sustainability, and manufacturing planning.
Supplies
Software:
- CAD: SolidWorks
- FEA: nTopology
- Documentation: Excel, Word
Hardware:
- 3D printer: FDM Printer (Prusa Slicer MINI+, MakerBot replicator 2)
Materials:
- PLA (Prototype) -1.75 mm Diameter
Problem Identification & Research
The survey and market analysis revealed common pain points in current desk organizers:
- Incompatible with circular or custom desk edges
- Magnetic holders pose a risk to electronics like SSDs/HDDs
- Scratches on desk surfaces from metallic parts
And my main goals were,
- Universal fit with rotating clamps
- Use of non-magnetic materials
- Include scratch-proof rubber padding
- Lightweight & eco-friendly final product
CAD Design & Innovation
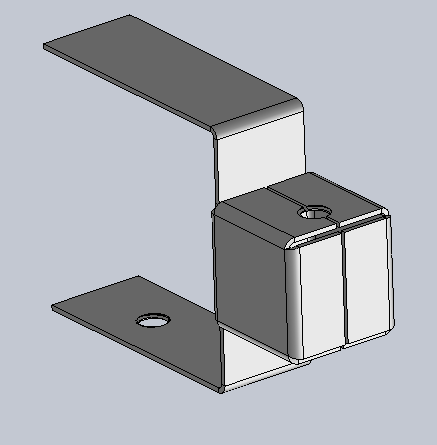
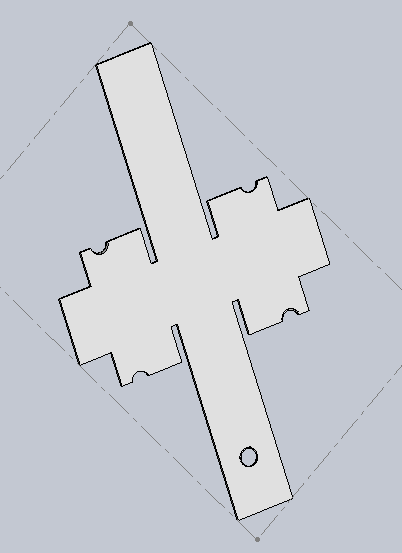
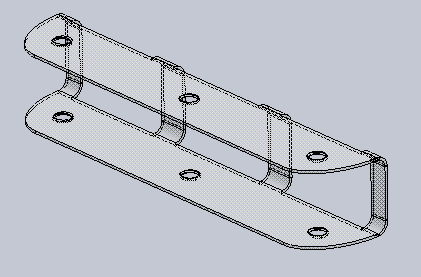
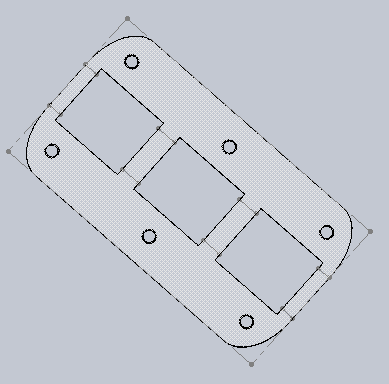
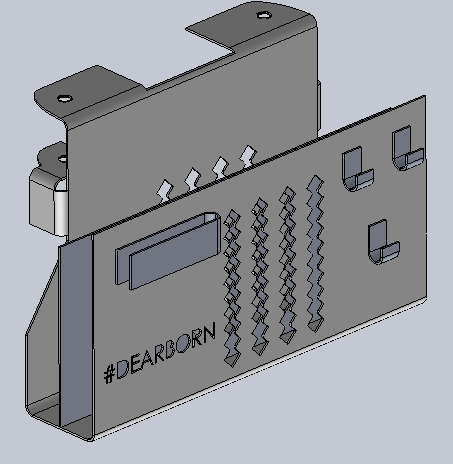
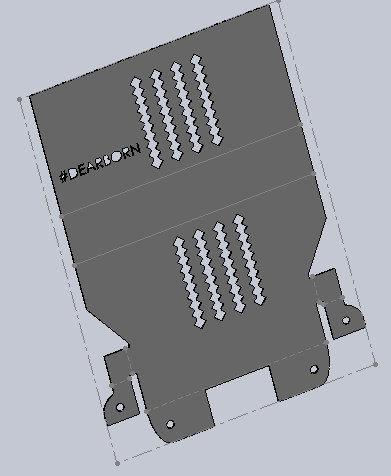



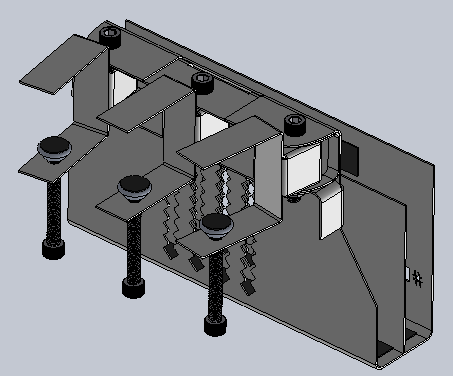
The prototype design evolved from a cross-clamp concept to a more compact rotating clip system, with angular motion up to 146°. The final prototype includes:
- Support Bar
- Two Rotating Clips
- Storage Compartment with Pen/ID Holders
For the final product, we have used aluminum 6061-T4 sheet metal. Initially, the clip and compartment parts were designed to be manufactured in casting. Later, considering design, weight, and cost, it was changed to sheet metal, as it is cost-effective and can be due to its formability. Which resulted in a reduced weight from more than 3 kg to 1.25 kg approximately. For the actual product, the rubber pads, allen bolts, nuts, and bolt covers with rubber pads and the main components, which are clips, a support bar, and a compartment. A separate sheet of metal parts is added in between two other small bending parts for pen and lanyard holders. Those parts can be welded to the compartment part.
3D Printing the Prototype


The prototype assembly is very simple, with only five parts. Except for the Allen bolt and nut, everything is made of PLA material. The support bar is the main component, with the two clips placed inside and the compartment placed outside with Allen bolts and nuts attached to it. Due to the prototype, the thickness is made to be 10 mm for better stiffness. After that, the Allen bolt with a cover needs to be placed within the two clips and attached to the clip attachment in the support bar. The clips can be rotated to a 146-degree angle to be clipped in both rectangular and circular surfaces.
Finite Element Analysis (FEA)
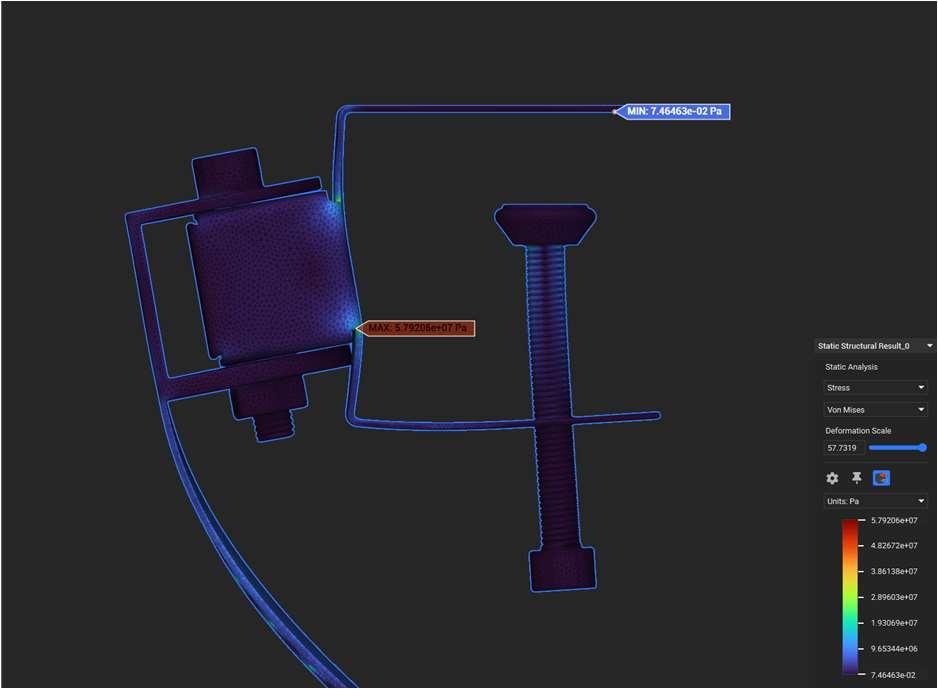
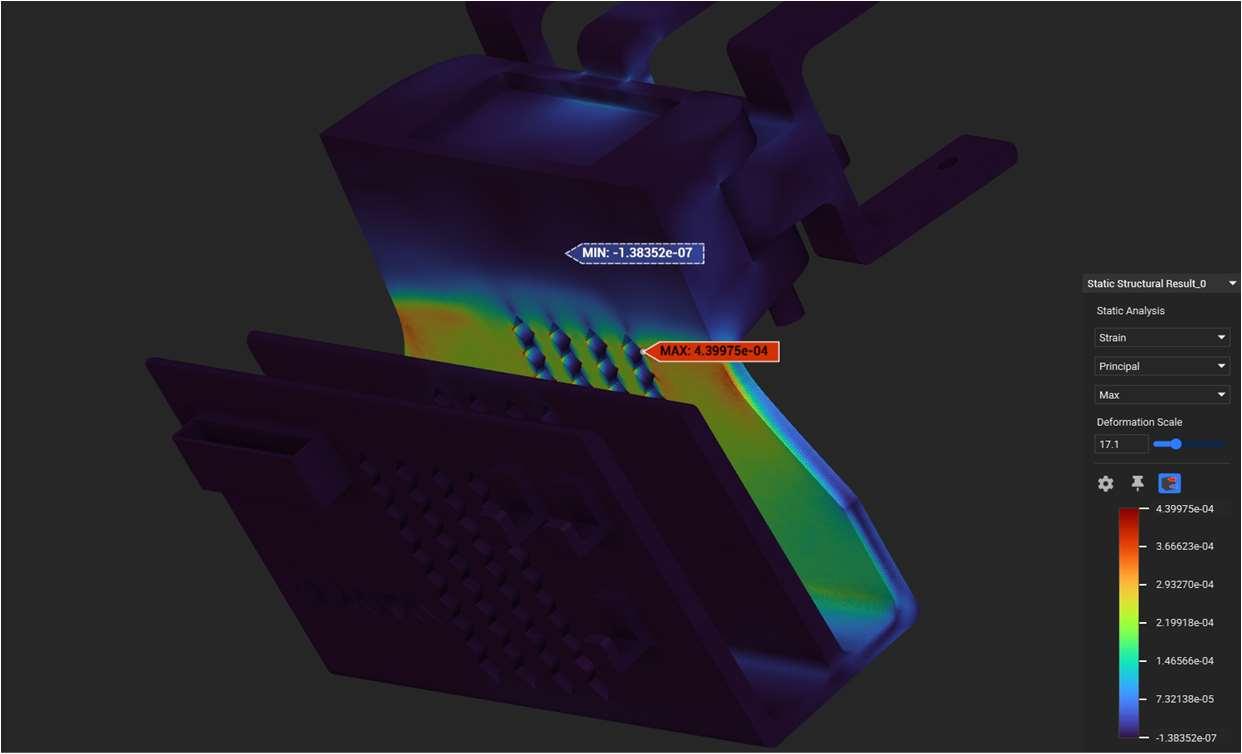
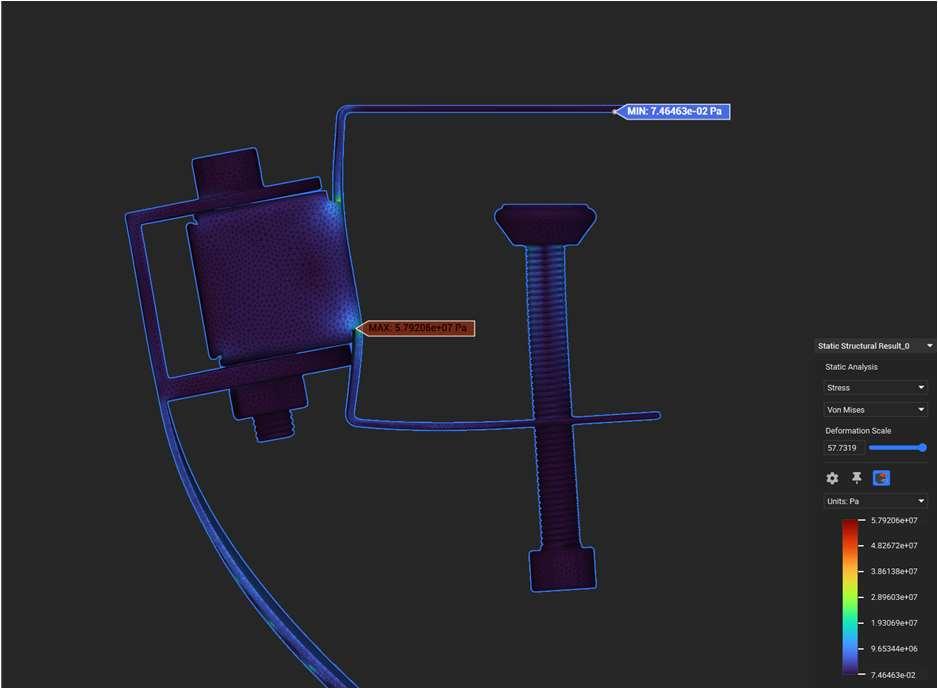
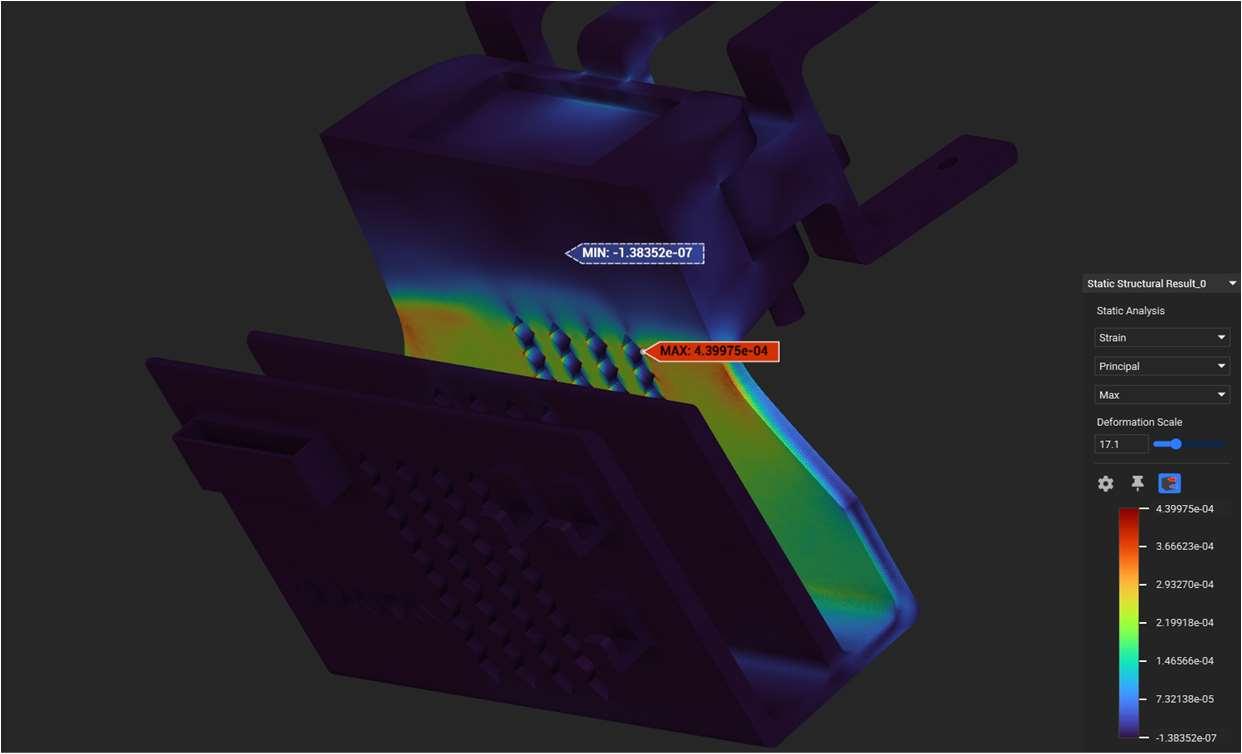
Prototype:
- Material: PLA
- Load: 30 N
- Software: nTopology
- Result: Stress concentrated near clamps; weight reduced from 3.2 kg to 2 kg
To simulate the model, nTopology Inc. was used with these simulation steps involving meshing the CAD body, applying material property, setting boundary constraints, loading application, and solving the model. The results are interpreted to evaluate maximum stress regions, strain distribution, and Factor of Safety (FoS) for durability. Key outcomes include critical stress points near clamps and the compartment. The objective is weight reduction. The first model for the prototype weighs nearly 3.2 kg, but with some design modification with the help of FEA analysis, we reduced the weight to 2 kg for the 3D-printed PLA. The below figure uses the newest design for the prototype, which sustains 50 newtons (breaking/bending moment), but it can sustain 30 newtons of force.
Final Product (Aluminum 6061-T4):
- Load: 50 N
- Material Properties:
- Young’s Modulus: 69 GPa
- Yield Strength: 275 MPa
- Result: Minimal deformation; High durability; Maintained elastic limit
The load conditions for the final model are static load and fixed constraint. The force applied is 50 Newton (11.24 lbs) on the compartment with equal loads, and the faces of the model that holds the table are fixed constraints. FEA software computed displacement, stress, and strain distributions across the model. The results showed minimal deformation under operational loads, with values near the clamp attachment points and edges of compartments. The strain analysis showed minimal deformation under operational loads, with localized strain increasing near clamps but remaining within elastic limits. Aluminum 6061-T4 is lightweight, strong, and resistant to deformation, making it an ideal candidate for optimization.
Assembly Process
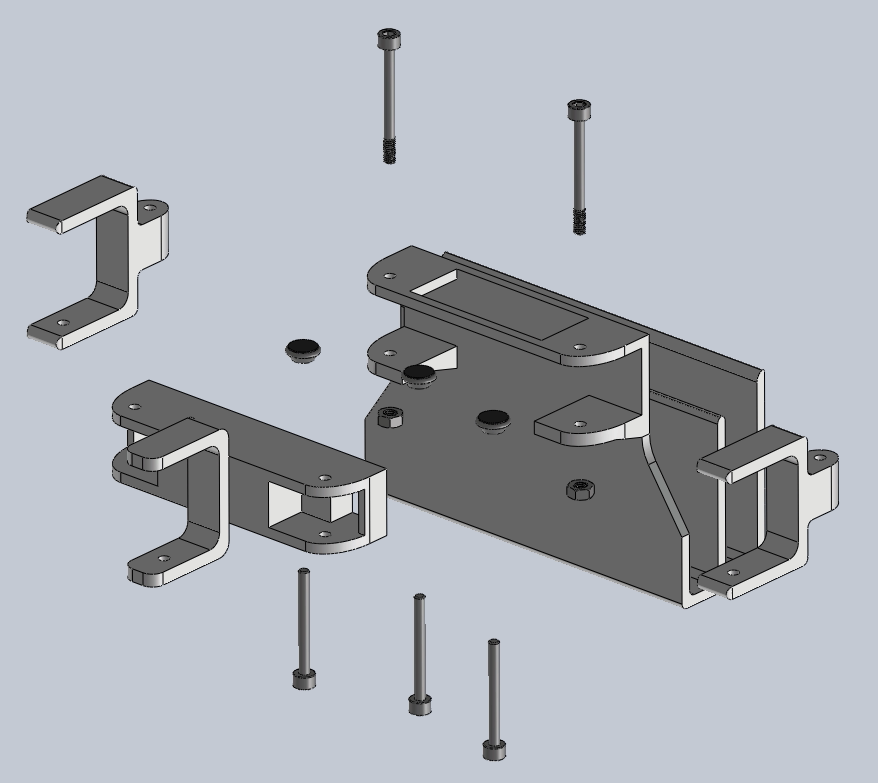
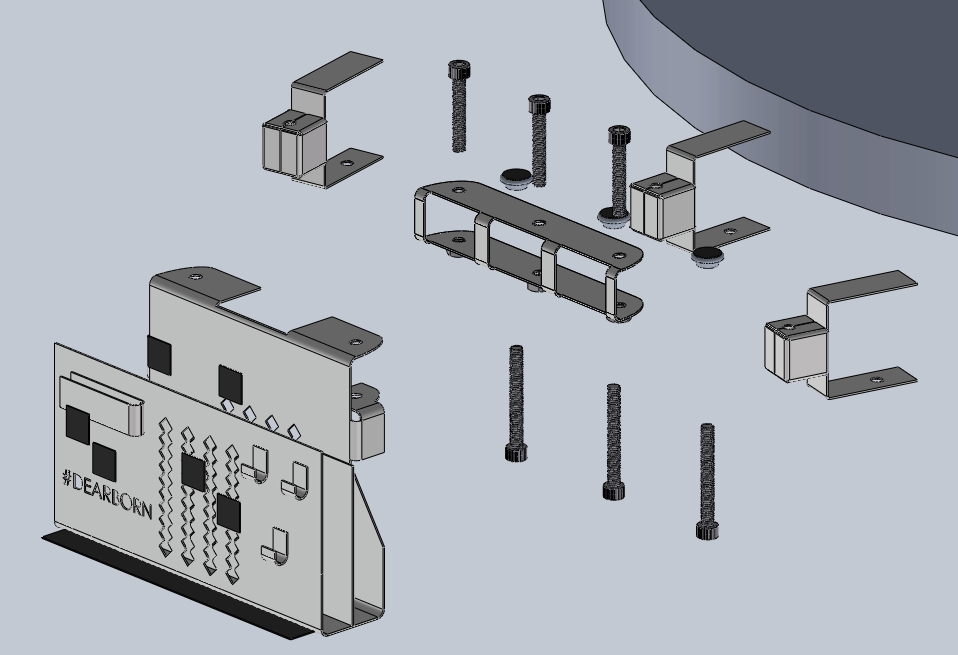
Parts:
- Support Bar
- 2 Rotating Clips
- Storage Compartment
- Allen bolts + nuts
- Pen & ID card holders (optional bent sheet parts)
Process:
- Insert clips into support bar slots
- Mount compartment over clips
- Fasten with Allen bolts
- Add rubber padding for anti-scratch
Environmental Impact & Sustainability
- Aluminum 6061-T4 is 95% recyclable
- Modular design reduces waste and simplifies repair
- Local sourcing reduced shipping footprint by 20%
- Life Cycle Analysis (LCA): lower CO₂ emissions, longer lifespan
Cost & Business Analysis
- Prototype Cost (PLA): $10
- Aluminum Version Cost: $30–35
- Selling Price: $40
- Break-Even Point: 700 units
- Manufacturing Strategy: Lean production, CNC automation, local supply chain
Conclusion
The AnyDesk Storage Organizer successfully bridges the gap between universal desk compatibility, aesthetic utility, and engineering precision. From CAD to 3D print to FEA to final aluminum fabrication, this project showcases an end-to-end digital manufacturing process with sustainability at its core.
What’s Next:
- IoT integration for smart desk features
- Extendable clips for thicker desk panels
- Custom finishes & anodized branding