Make Improved Electrical Crimp Terminal Connections
by Bill WW in Circuits > Electronics
10850 Views, 9 Favorites, 0 Comments
Make Improved Electrical Crimp Terminal Connections
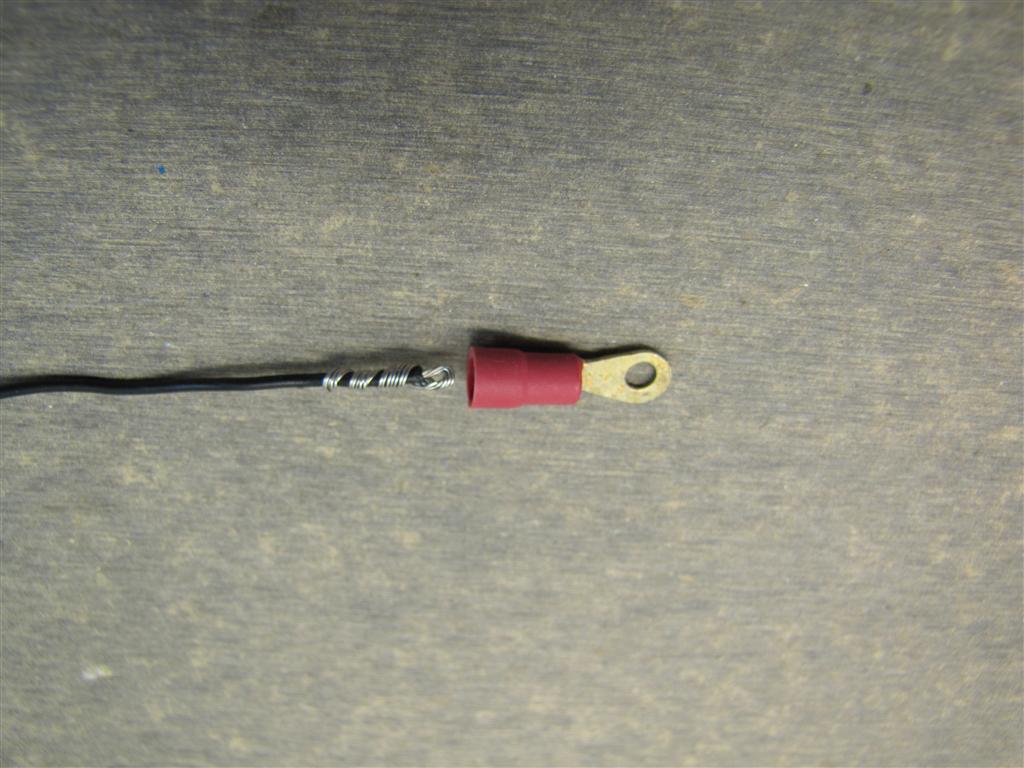.JPG)
Crimp terminals and butt connectors are pretty common in electrical and electronic projects, but using them successfully on small wire sizes can be tricky. And hookup wires for robotics and miniature controllers can be pretty tiny. Another common problem with crimp terminals is that with a bit of flexing, the bare wire can break right at the terminal.
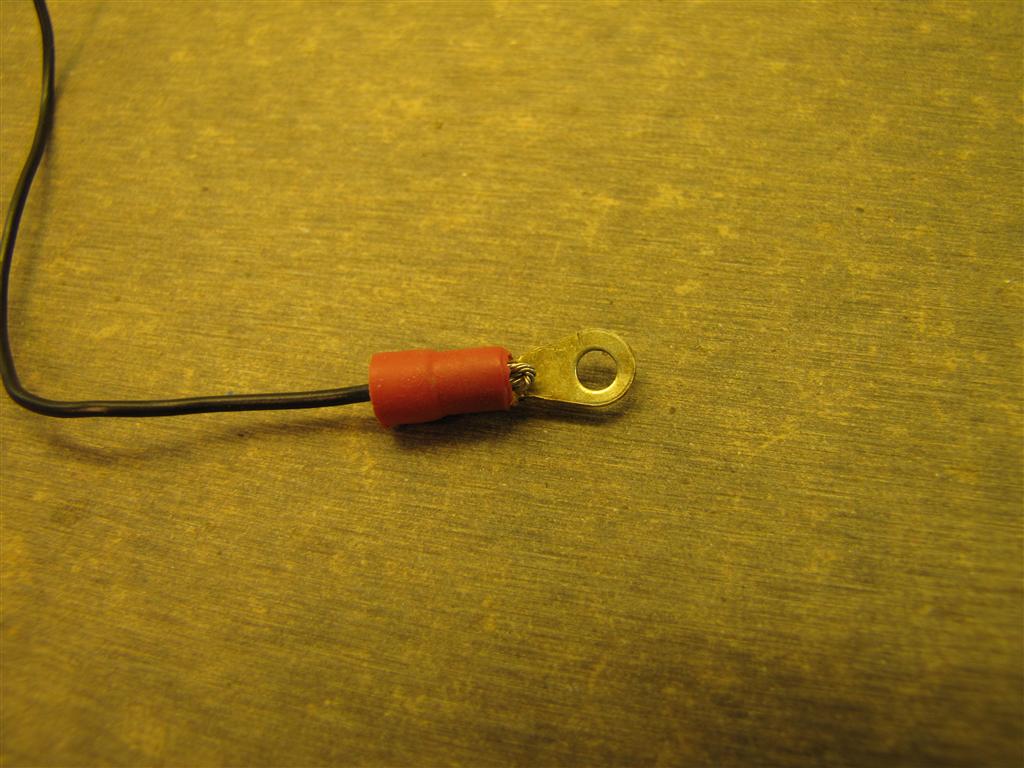.JPG)
Parts and tools.
The "parts" involved are the small crimp style terminals and butt connectors often used in electrical and electronic projects. They are commonly aviailabe in three color coded sizes, red is the smallest, then blue, then yellow. Wire gauge size range is always shown on the packaging.
A crimping tool is available, but in a pinch the crimp can be made with your pliers.
The "parts" involved are the small crimp style terminals and butt connectors often used in electrical and electronic projects. They are commonly aviailabe in three color coded sizes, red is the smallest, then blue, then yellow. Wire gauge size range is always shown on the packaging.
A crimping tool is available, but in a pinch the crimp can be made with your pliers.
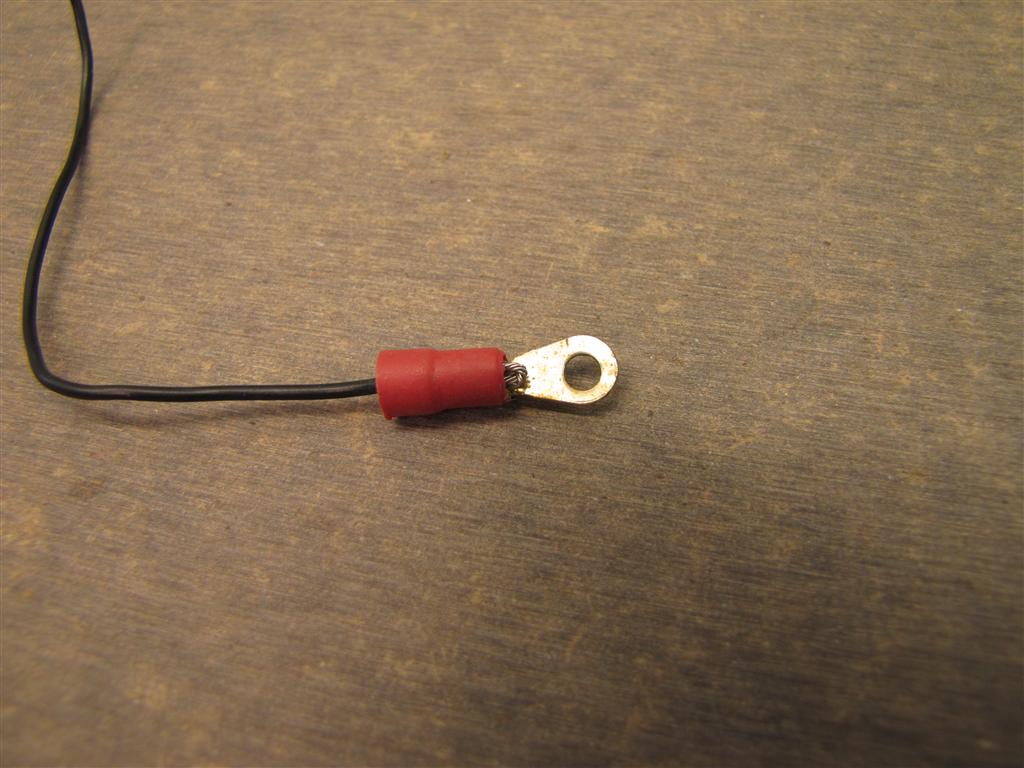.JPG)
The problem: Failures can occur from using too large a terminal for the wire size; using too much force on the crimping tool; and due to vibration breaking the wire right at the terminal. Also, at times you want to use a butt connector to connect two different wire sizes.
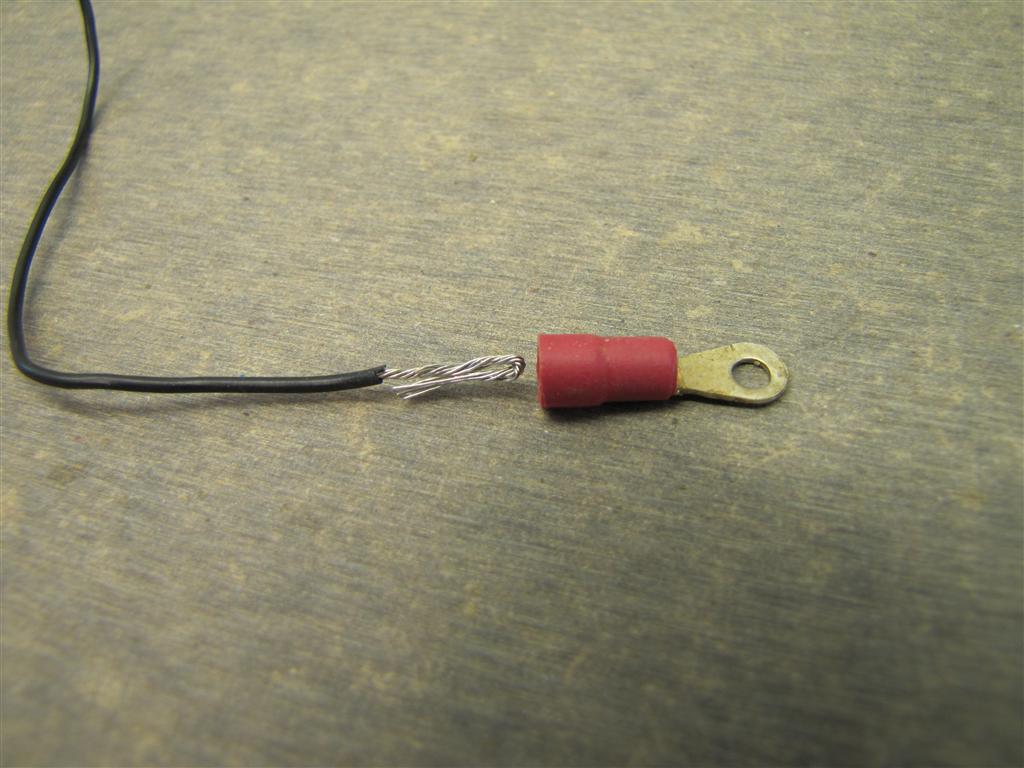.JPG)
Solution #1: To ensure a better connection when working with small wire sizes, just strip the insulation a bit fmore and double over the wire connector, as in the photo. This provides more wire for the terminal to crimp onto. Ideally, the wire should be snug when inserted into the terminal.
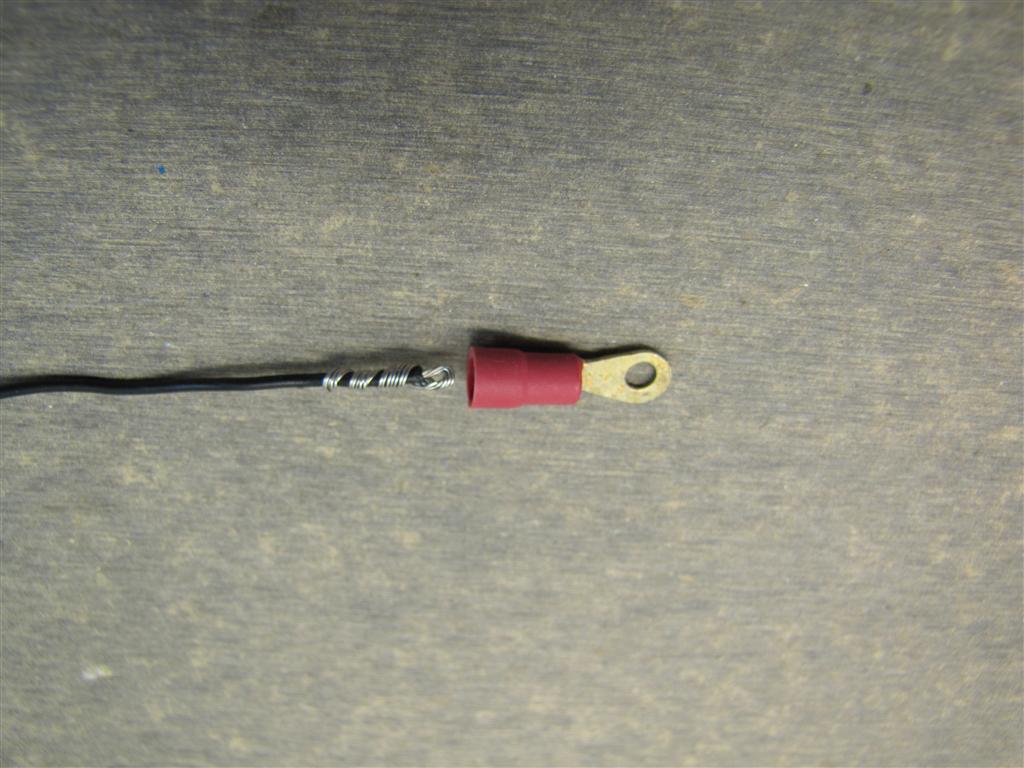.JPG)
Sollution #2: Fix for wire fatigue and breakage at terminal:
The bare wire can break at the terminal, especially small wires ans any time there is flexing.
This can be solved by stripping about 1/2" of insulation, then winding the bare wire back around the insulation before inserting it into the terminal. The wire-over-insulation adds a lot of strength.
The bare wire can break at the terminal, especially small wires ans any time there is flexing.
This can be solved by stripping about 1/2" of insulation, then winding the bare wire back around the insulation before inserting it into the terminal. The wire-over-insulation adds a lot of strength.