Metal Star Puzzle
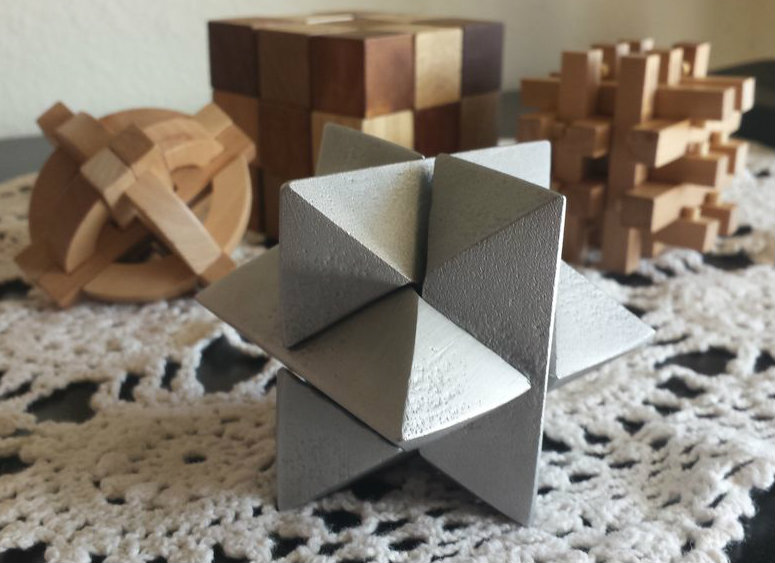
I like puzzles. It is fun to take something apart and try to put it back together again. I can spend days sometimes weeks trying to figure out a puzzle if it provides a formidable challenge.
After enjoying some puzzling, I had an inkling to make my own. I don't claim this design as my own, it has been around for some time. I just think it looks really cool and also makes a good paper weight. The following is my endeavors to make a metal star puzzle.
Design
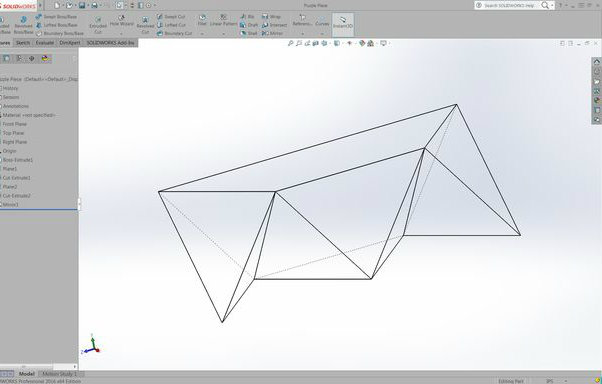
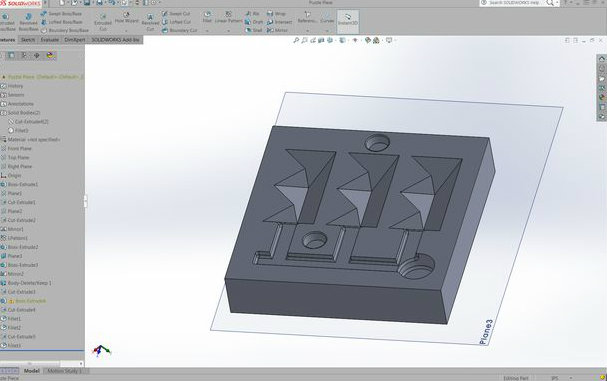
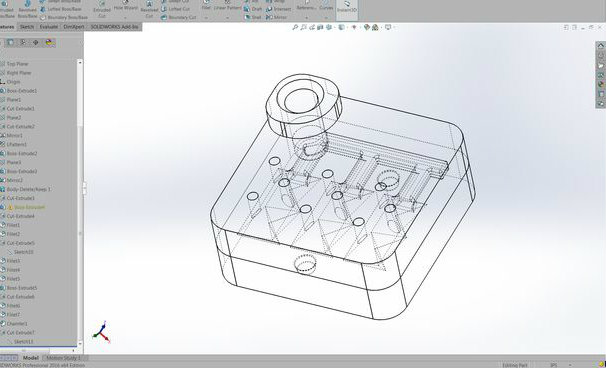
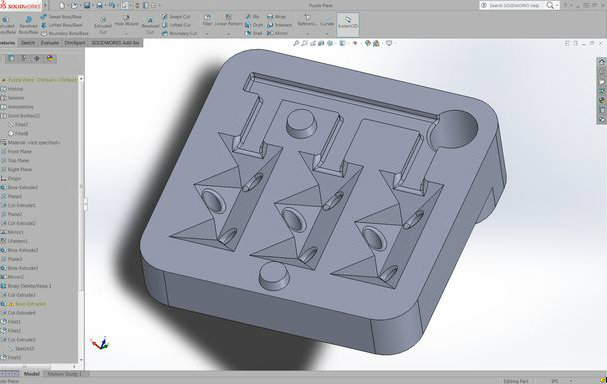
The metal star puzzle consists of 6 interlocking pieces. All of them are clones of one another. I have seen some designs where you have 3, 2, and 1; I find that version of this puzzle to be not quite as elegant as this one I'm making (the solution anyways).
I designed the piece of the puzzle in Solidworks. My intention was to 3d print a sand mold that I could use to cast these into aluminum. After designing the one piece, I repeated it and modeled a negative of it, creating a model of the mold design.
The files for the mold and the 1 piece are attached to this step. Feel free to use them for 3d printing purposes or whatever you'd like.
Printing the Mold



After completing the mold design, I uploaded the files to my companies sand printer and built 2 molds, 4 halves in total. You can view my other instructables for more details on the molding and printing processes I used. It took 5 hours to print the mold, most of that time is just waiting for the glue to fully bond with the sand grains.
Casting and Cleaning






Once the mold was printed, it was brought out to the melting line and prepped for pouring. Weights are placed on it so the top half of the mold does not lift off and spill metal out the sides. I pour this out of 319 aluminum at 1300F, very weak metal but strength is not important for this project.
After the metal has cooled, the castings were broken out of the molds, cut from the feeding system, ground down, and sandblasted to a consistent finish. The casting and cleaning process took 2 hours.
Disassembly


Once made taking it apart is very simple......
Assembly
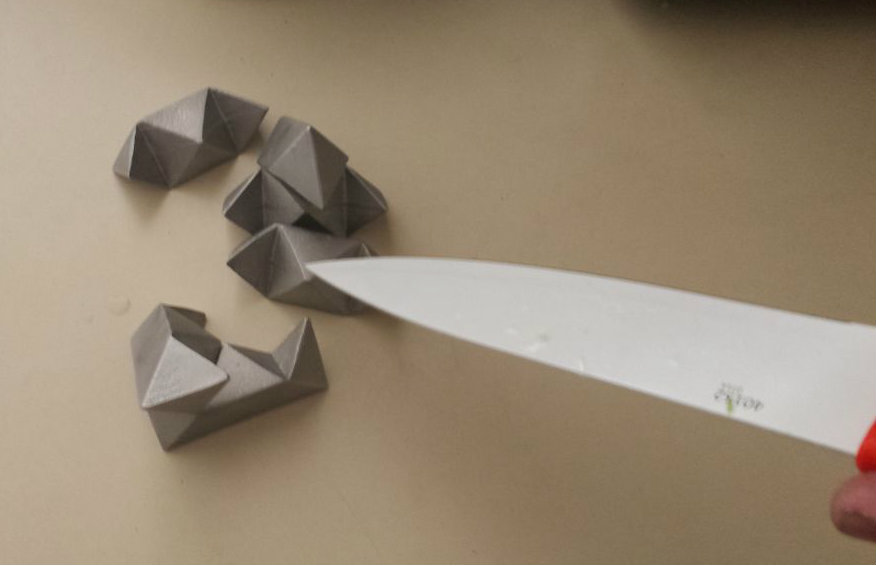

I am not posting the solution, I always like trying to figure things out on my own so I encourage you to as well if you decide to make some sort of iteration of this one. I can give you a hint though. The pieces are not assembled one at a time.
If you like this, please vote for it in the metal contest.