Panneau Fumant - Promotion Du Fablab Dans L'espace Urbain.
by QuentinKhamiscc095 in Workshop > 3D Printing
48 Views, 2 Favorites, 0 Comments
Panneau Fumant - Promotion Du Fablab Dans L'espace Urbain.

Dans le cadre de notre projet au FabLab Descartes, nous avons conçu un panneau signalétique innovant combinant artisanat numérique et low-tech. Construit en bois, découpé au laser pour une fabrication précise et reproductible, ce dispositif intègre un système de fumée à eau écologique, activé par une minuterie programmable via Arduino. L'objectif est de créer une signalétique dynamique qui capte l'attention et guide visuellement les visiteurs vers notre FabLab.
Le panneau fonctionne grâce à un brumisateurs ultrasoniques alimenté par une batterie LiPo rechargeable, elle-même alimentée par un petit panneau solaire intégré. Cette solution énergétique autonome permet des diffusions de fumée programmables, avec possibilité d'adapter la fréquence et la durée des émissions selon les besoins. Le panneau en bois, enduit d’une peinture orange hydrofuge, permet de résister aux intempéries tout en conservant un aspect original et artisanal.
Ce panneau crée une signature visuelle unique pour notre FabLab. La fumée froide, totalement inoffensive pour la planète, produit un effet à la fois ludique et intriguant, suscitant la curiosité des passants.
Supplies
Une liste complète des matériaux est à télécharger dans cette rubrique.
Pour notre Projet, nous voulions nous servir un maximum des services que propose le FabLab, ainsi nous avons utilisé les machines et logiciels suivant :
Machines => Fraiseuse, Découpe laser, Découpe vinyle, Imprimante 3D.
Logiciels => Inkscape, Arduino Uno, Fusion 360.
Matériel nécessaire à la conception et fabrication de l’ensemble du panneau fumant :
Structure
- Planche de bois 80cm*35cm photo planche
- Papier autocollant, Papier transfert,
Boîtier technique - Modélisé sous Fusion 360, ce compartiment étanche intègre :
- Le fichier à télécharger du boîtier technique
- Un réservoir d'eau de 21*3*7 cm
- La carte Arduino Uno avec son shield de contrôle
- Les brumisateurs ultrasoniques ( 3 unités) - Référence : Module atomiseur d'eau à ultrasons 101020090
- L'ensemble du câblage électrique
Fixation du panneau fumant adaptable :
- Accroches Serflex
- Poteau
Imperméabilisation du panneau en bois
- Peinture hydrofuge (couleur au choix)
Alimentation
- Batterie Externe Solaire 20000MAH
Première Vu Du Panneau, Support Pour Illustrer Nos Idées.
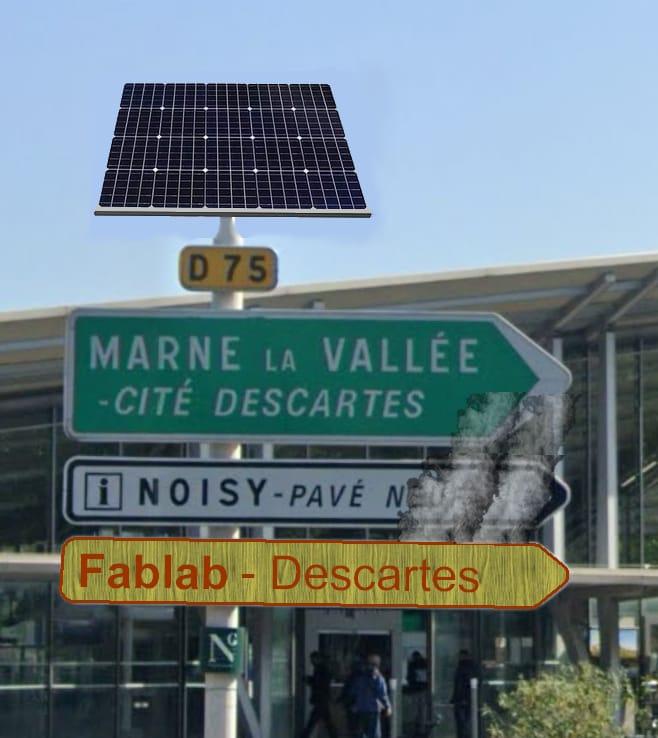.jpg)
.png)
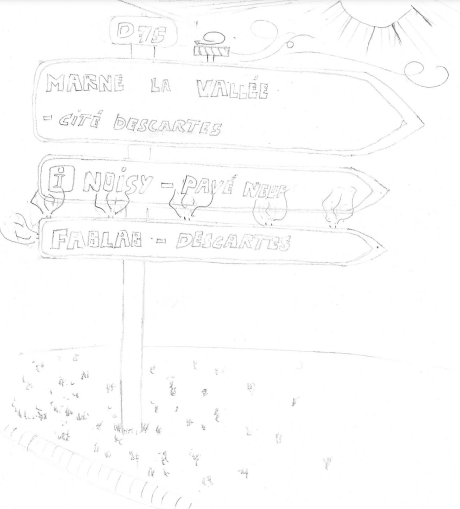.png)
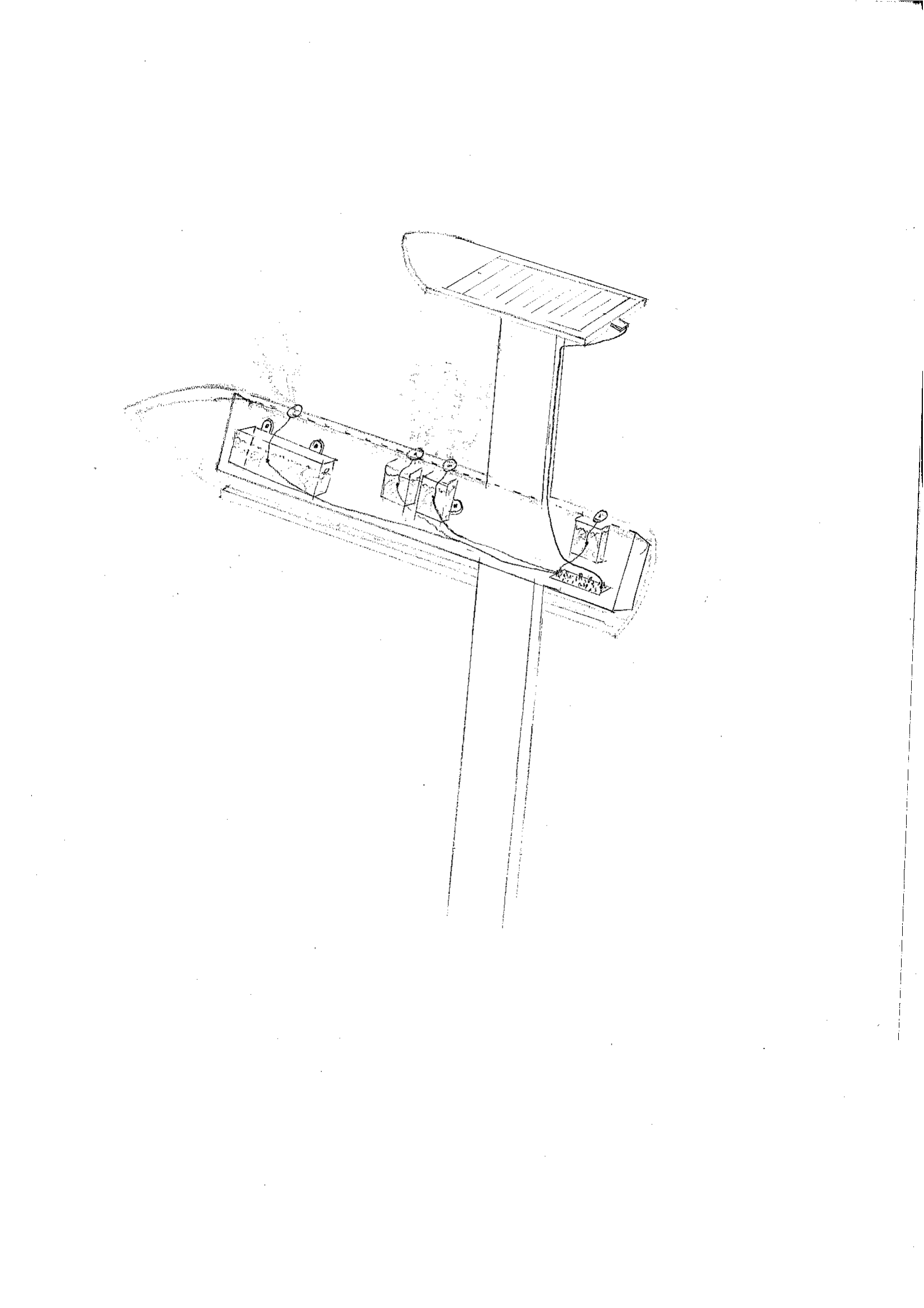
Visualisation du panneau fumant dans son environnement - Première approche de présentation - Non essentielle à la fabrication.
Nous avons voulu voir comment le panneau fumant pourrait s’intégrer dans son environnement. nous nous sommes inspiré d'un panneau de circulation indiquant une ville par exemple.
Pour avoir un support de présentation, on prend une photo de ce même panneau et on l'arrange avec le logiciel Photofiltre, on modifie le panneau pour obtenir un effet bois, puis on ajoute le texte que l’on souhaite écrire (ici "FabLab - Descartes") sur le panneau. Les coloris sont choisis à partir des fonds proposés par le logiciel.
Photofiltre qui permet la gestion de calques, permet d’ajouter des images sur notre fond. Nous ajoutons un panneau solaire sur la présentation, il servira à alimenter les brumisateurs. Sur le même principe, on ajoute une image de vapeur d’eau . Avec les outils du logiciel permettant de recadrer les calques, nous utilisons la fonction d’opacité qui joue sur la transparence des calques, les calques sont fusionnés avec le fond. Il suffit alors de flouter les transitions entre les images afin qu’elles soient plus douces, et nous obtenons notre image de panneau. (voir Photo 2)
Après avoir fait naître le projet dans nos têtes nous devions aussi fixer nos idées sur papiers pour faire comprendre nos intentions, notre but. Le dessin et les croquis d’ambiance nous ont permis de dialoguer avec un public montrer visuellement à quoi nous aspirerions et le convaincre. Cette phase se révèle importante et décisive pour faire valider notre projet. On se doit alors d’être clair.
Voici les esquisses que nous proposons pour le projet
Le Rétroplanning
Voici le Rétroplanning que nous nous sommes fixés pour parvenir à notre projet dans les temps, les sessions de cours durent 7h, à chaque jour il faut compter 7h de production à 3 personnes.
12/03 - Études préliminaires & définition du concept
- Étude des contraintes techniques et environnementales
- Validation des matériaux (bois/métal pour le panneau, composants électroniques, récupération d’eau)
- Finalisation du design esthétique et technique
19/03 - Fabrication des composants individuels
- Impression 3D des pièces (cache des pièces techniques, récupérateur d’eau)
- Fabrication de la structure du panneau (bois/métal)
- teste avec un chargeur solaire et des circuits électriques
26/03 - Programmation & calibrage
- Développement du code Arduino pour contrôler la fumée sur minuterie
- Ajustements du système pour optimiser l'effet visuel
- Modélisation et simulation
- Modélisation du panneau et des composants sur Fusion 360
- Simulation du système de récupération d’eau et de génération de fumée
- Validation des plans définitifs avant fabrication
02/04 - Montage du récupérateur d’eau et intégration au panneau
- Raccordement du panneau à la source d’énergie solaire
- Installation du système de génération de fumée et premier test de fonctionnement
09/04Tests et validation
- Tests unitaires (autonomie du panneau solaire, production de fumée, détection des passants)
- Ajustements techniques et corrections éventuelles
10/04 Présentation grand public 🎉
La Programmation - Arduino Uno


Dans le cadre de notre projet de panneau signalétique fumant, nous avons engagé une démarche de conception qui s'est articulée autour de plusieurs phases clés. Tout d'abord, nous avons été formés sur les aspects fondamentaux de la programmation Arduino Uno, pendant 6h au FabLab Descartes. Cette formation comprenait la gestion des entrées-sorties numériques jusqu'à l'intégration de capteurs complexes.
Face au défi technique de la production de fumée, nous avons mené une étude entre deux solutions de production de fumée.
La première option, basée sur la glycérine, offrait certes une fumée plus dense mais présentait des inconvénients majeurs en termes d'approvisionnement en consommables et de maintenance régulière.
La seconde solution, utilisant des brumisateurs ultrasoniques, s'est révélée bien plus adaptée à nos besoins grâce à son fonctionnement simplifié ne nécessitant que de l'eau, son caractère écologique et sa facilité d'intégration avec notre système Arduino.
Notre choix s'est finalement porté sur des brumisateurs ultrasoniques 12V. Les principaux facteurs déterminants ont été leur faible consommation énergétique (inférieure à 15W), leur sécurité d'utilisation (absence de risque de surchauffe) et la consommation d'eau très fiable. Ce choix technique nous a permis de développer un système à la fois performant et durable, parfaitement aligné avec les valeurs d'innovation responsable que nous souhaitions dans ce projet. Il fallait donc programmer les Brumisateurs via une carte Arduino Uno alimentée par une batterie externe solaire.
La mise en œuvre a nécessité la conception d'un circuit électronique sur mesure. L'ensemble du système a été pensé pour que tous l'ensemble s'emboîte, avec des connecteurs et un boîtier permettant un accès rapide à tous les composants.
Sélection des Composants
- Carte Arduino Uno
- Module Relais - Shift pour simplifier les branchements
- réservoir d’eau
- Batterie Externe Solaire ( ou autre source d’énergie)
Objectifs :
- Activer les brumisateurs par cycles toutes les 10s pendant 5s
- Sécuriser le système
- Connexion de 3 brumisateurs ultrasons à la carte Arduino (broches A3, A2, 5)
- Branchement de l’alimentation (USB ou batterie externe)
- Test individuel de chaque brumisateur pour s'assurer du bon fonctionnement
Le codage - Le Code
- Programmation de la carte Arduino avec le code suivant :
- Téléversement du code via Arduino IDE
Tests et ajustements
- Vérification du bon déclenchement des brumisateurs.
- Contrôle de la diffusion de fumée.
- Ajustement du positionnement et de la hauteur des brumisateurs pour une meilleure diffusion, il ne doivent pas tremper.
Downloads
Dimensionnement Des Composantes
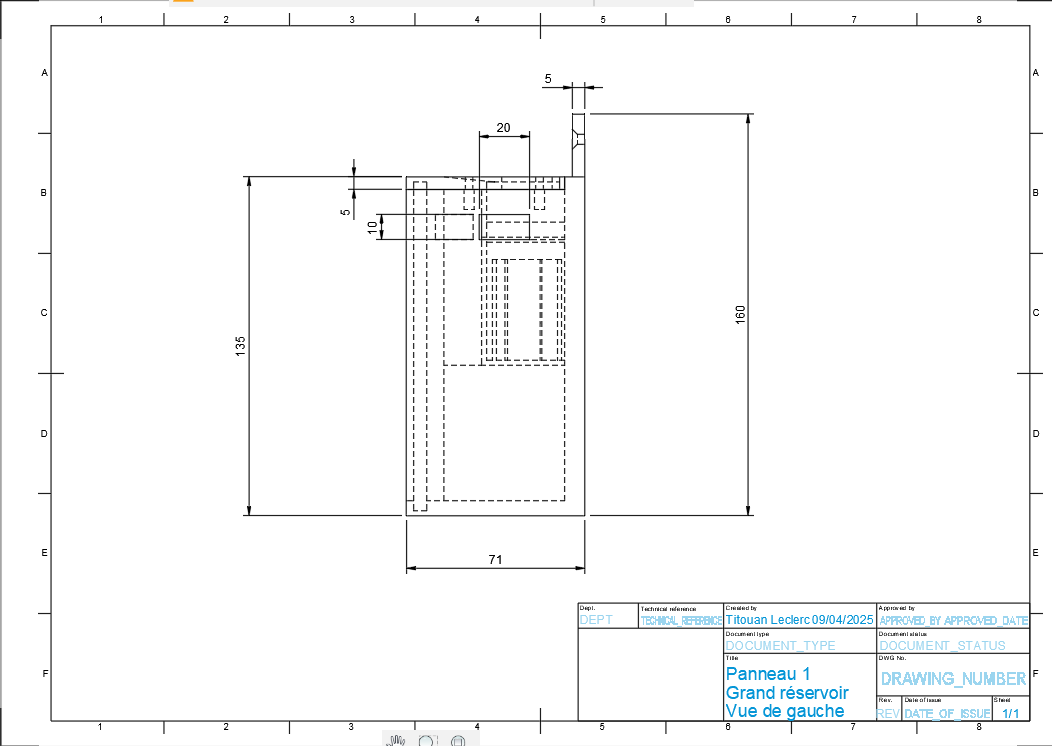
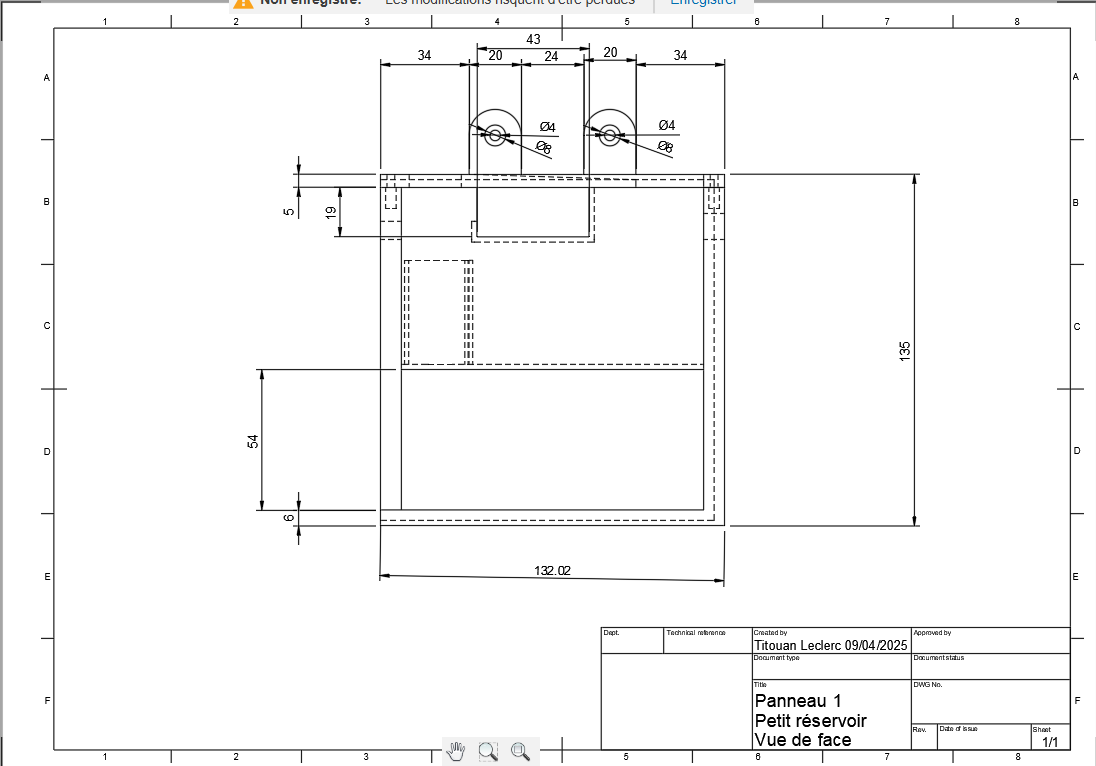
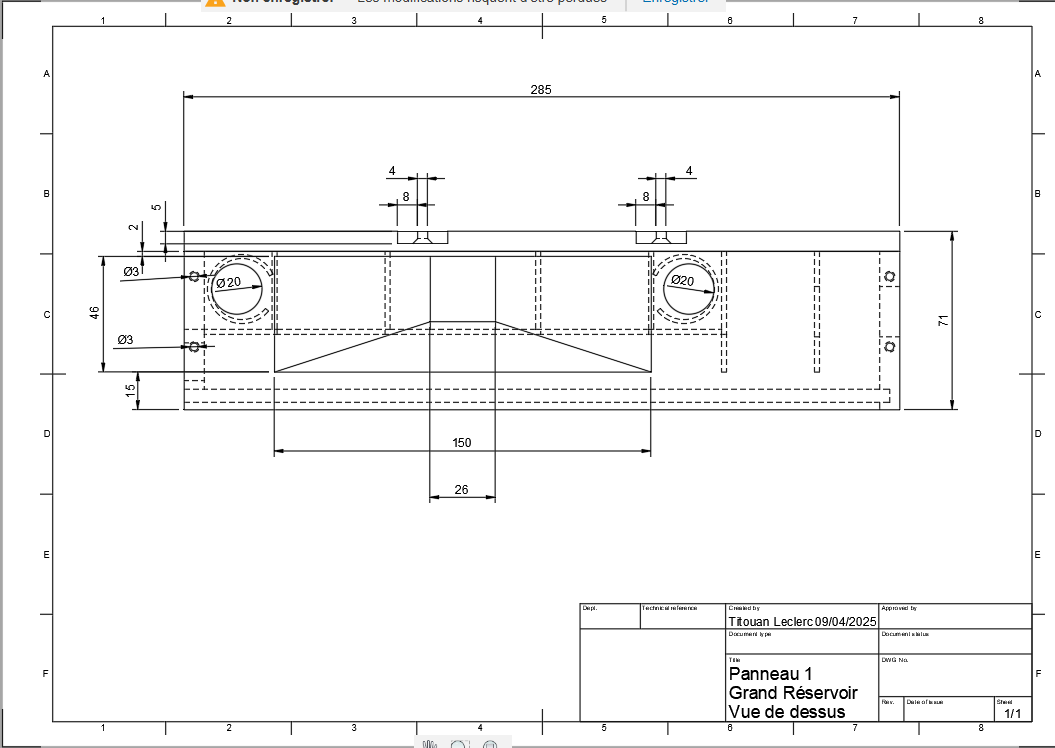
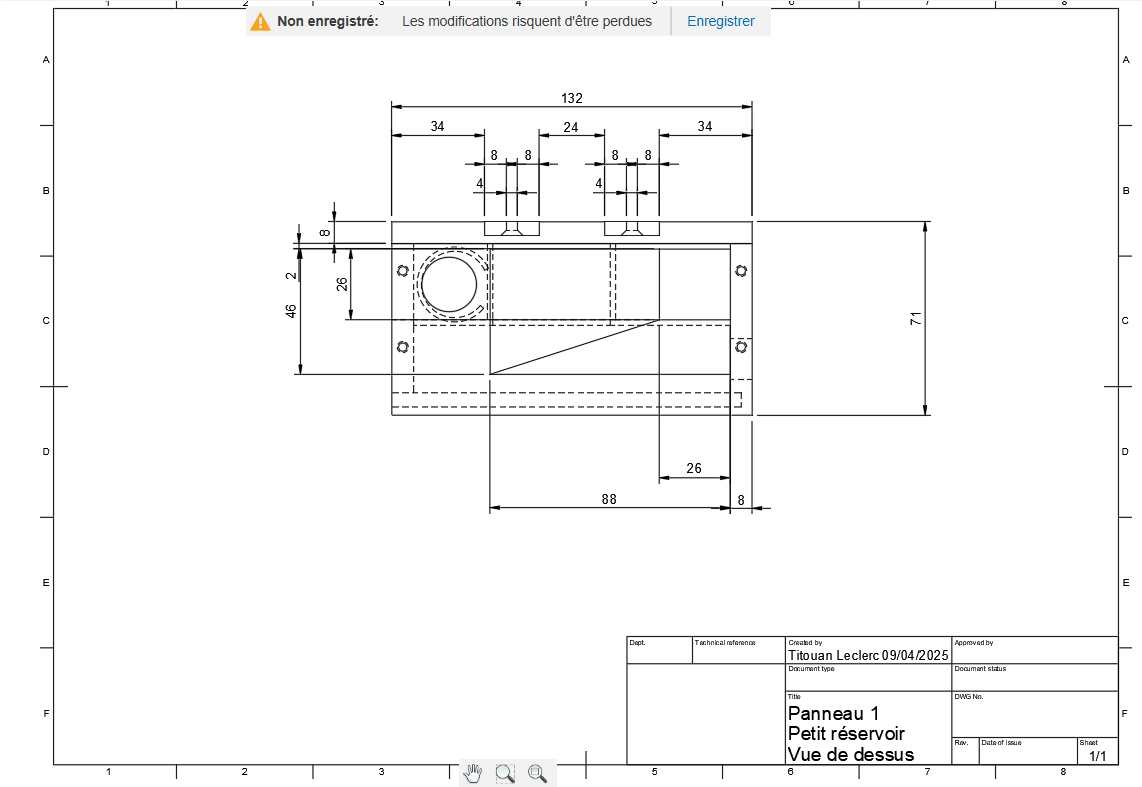
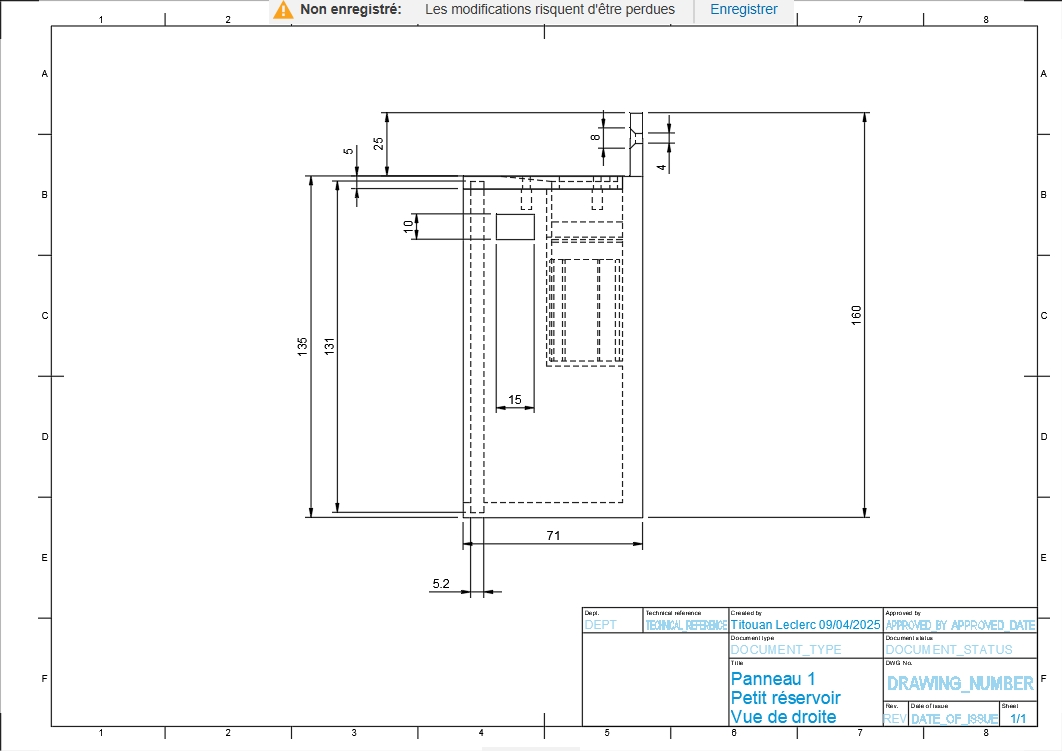
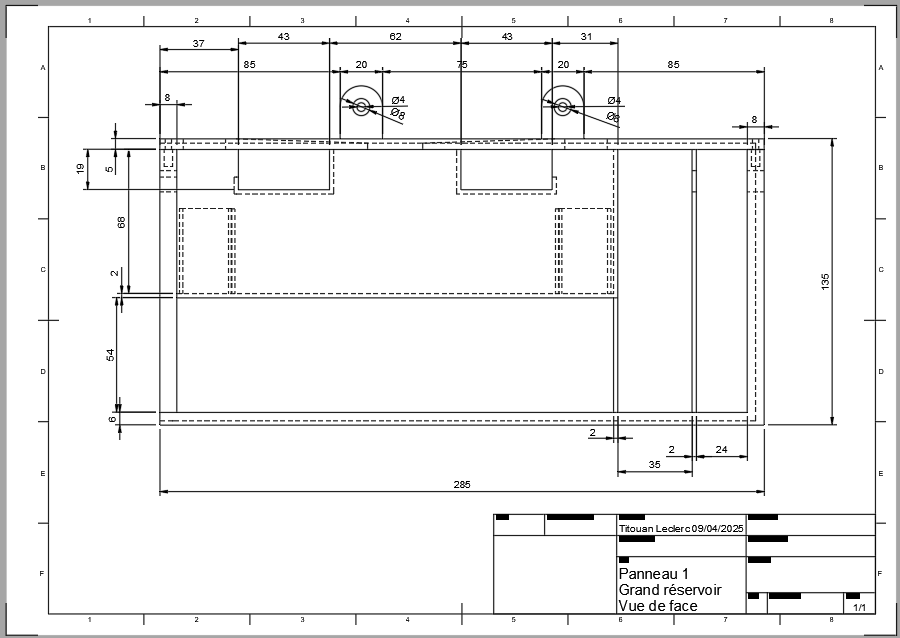
On est parti sur des tailles de composantes qui ont évoluées avec le temps pour s'adapter au mieux à notre projet.
Les réservoirs
Afin de pouvoir loger les différentes pièces électroniques nécessaires pour produire de la vapeur d’eau mais aussi le stockage, nous avons décidé de produire nous-même les réservoirs. La modélisation des réservoirs s’est effectuée sur le logiciel Fusion 360, vu en cours (étape 4)
Le panneau
Pour les dimensions du panneau, nous sommes partie de l'étape 1 avec les dimensions d'un panneau de circulations réel : 2m de long, 1m de large sur 10cm d'épaisseur. Après discussion avec l'équipe du FabLab, nous avons modifié ces dimensions pour des raisons de faisabilité. Ce choix de réduction de taille du panneau s’est fait car nous avons réaliser qu'un passant se sent d'autant plus concerné par un panneau qui est proportionnel à sa taille qu'un panneau trop grand. Le panneau reste tout de même visible pour les automobilistes. Aussi, nous avons voulu au maximum utiliser des matériaux à ré-employables. Nous avons opté pour des planches de bois contre-plaquées que nous avons trouvée au FabLab. La taille finale est de 80cm de long pour 35cm de large sur 1cm d'épaisseur.
Le boîtier technique
Le boîtier technique à été réaliser sur mesure pour qu'il réponde parfaitement à notre projet et au visuel attendu, aux contraintes auxquelles nous avons fait face (potentiel poteau à prendre en compte, récupération d'eau, alimentation autonome en énergie, gestion de la fumée, esthétique...). Il se nomme boîtier technique car il comprend plusieurs parties avec des fonctions propres qui s'encastrent en un ensemble. Les différentes parties sont : un grand réservoir d'eau de 21*7*3cm, deux emplacements pour mettre les composantes électroniques à l'abri de l'eau, une partie de stockage vide, un couvercle qui permet l'échappement de la fumée et la récupération de l'eau. Le tout forme un ensemble soudé et fermé qui permet la sécurité de l'ensemble, protégé du vandalisme.
Il faut savoir que le "boîtier technique" se compose de ensembles, un central comprenant la carte Arduino, un grand réservoir prévu pour 2 brumisateurs et une annexe, séparée de ce dernier, a été conçue pour faire face au défi d'adaptabilité d'accroche au poteau dans un environnement extérieur.
Le boîtier technique majeur
- le Grand Réservoir 21*7*3cm
Au départ, nous avions prévu de faire des réservoirs séparées pour brumisateur. Toutefois, au vu des contraintes imposés notamment répartir les sorties de fumées, nous sommes partis sur deux réservoirs pouvant à la fois stocker l’eau et les appareils électroniques de manière distinct. Le boîtier technique majeur comprend donc le grand réservoir accueillant 2 brumisateurs, les composants électroniques qui font la jonction entre le Brumisateur et la carte Arduino, la carte Arduino avec son Shild.
- Les espaces pour la carte Arduino Uno et les cartes "Arduino-brumisateur"
Ces espaces sont inclus dans le boîtier technique majeur. C'est la carte Arduino Uno qui fait augmenter considérablement la taille du boîtier technique majeur.
Le boîtier technique mineur
- Petit réservoir 11,5*5*3cm (fait parti du "boîtier technique mineur") (voir photo)
Le petit réservoir est une copie du grand réservoir, à partir duquel nous divisé par 2 sa taille en retirant l’emplacement de la carte Arduino majeure.
- Les espaces pour les cartes "Arduino-brumisateur"
Dans les deux boîtiers techniques
- Portes coulissantes
Afin de pouvoir accéder aux au corps des boîtiers techniques, nous avons ajouté un système de porte coulissante. Elles sont en bois pour imprimer le moins possible de plastique. Nous les avons réalisés avec le logiciel Inkscape pour pouvoir faire lire le fichier par la machine "découpe laser" afin qu'elle découpe nettement les portes car elles doivent coulisser dans un rail dans la pièce finie.
- Couvercle multifonctions : Trou eau - Trou fumée
Nous devions recréer un couvercle pour fermer notre boîtier technique pour des raisons de protection des composantes électroniques ainsi que de prévenir du vandalisme possible. Ces couvercles servent à fermer les boîtiers techniques respectivement par le haut. Nous avons conçu des couvercles "techniques" dans le sens où ils ont plusieurs fonctions. La fonction principale est de fermer et protéger l'ensemble, ensuite ils sont ajourés pour laisser sortir la fumée des brumisateurs, on peut caractériser cette fonction de cheminée. Enfin, un autre trou est réservé à la récupération d'eau pour remplir le réservoir connecté par gravité. Autour de ce trou, des pentes ont été pensé pour guider l'eau jusqu'au trou.
Modélisation 3D

Pour la modélisation 3D des boîtiers techniques, nous avons procédés sur Fusion 360.
Nous étions débutants dans le domaine de la modélisation, grâce à un formation de l'équipe du FabLab Descartes sur bases et fondamentaux du logiciel, Fusion 360 nous était accessible et compréhensible pour la réalisation de nos pièces sur mesures.
Avec autant de composantes à l'intérieur des boîtiers de devions procéder avec méthode pour arriver à caler et penser à toutes nos parties techniques.
Pour éviter de vous embrouiller, vous retrouverez ci-joins les étapes majeures par lesquelles sont sommes passés pour confectionner nos boîtiers techniques et nous vous proposons de mettre en ligne le lien du boîtier majeur et mineur prêts à être imprimer par imprimante 3D.
La méthode/recommandations de manière succincte :
- Commencer à plat (plan x;y) pour faire une face avec toutes les composantes possibles toujours à plat.
- Une fois la face complète, commencer à étirer toutes les pièces techniques de ensemble. Vous travaillerez donc en 3D à partir de ce moment là et vous aurez introduit un axe z (les côtes) à votre plan.
- N'oubiler pas de travailler sur les faces que vous avez étirées.
- Travailler séparément de la pièce principale si nécéssaire pour vous faciliter le travail (couvercle). Vous pourrez ensuite scinder les éléments ensemble.
Design Du Panneau De Bois







Comme dit précédemment, les dimensions et formes du panneau ont évolué en fonctions des contraintes du projet. Comme les autres éléments visuels, le design du panneau à aussi changer fonction des attentes du FabLab Descartes et des disponibilités de matériaux.
Nous souhaitions réaliser un panneau avec un style "entrée de ville" avec un liserai rouge sur fond blanc. L'effet escompté était de faire rentrer en immersion la personne voyant le panneau, qu'à la vue de se dernier il croit qu'il rentre dans la ville du Fablab Descartes.
Le projet a ensuite changé. Sur un point de vue technique, tout était correct pour l'impression, jusqu'au moment de la vérification des stocks, il n'y avait pas de papiers autocollants rouge sur fond blanc. Alors, notre équipe a du s'adapter et faire preuve de créativité ; avec Thomas nous avons regarder le stock et trouvé une peinture orange vermillon, la couleur emblématique du Fablab. Nous décidons de peindre le panneau en ce orange et de coller des autocollants blancs. Les modifications se sont faites par Inkscape, effectuées en 5min.
Pour réaliser ce panneau, nous nous sommes servis de de Inkscape pour plusieurs raisons ;
- Pouvoir envoyer le ficher et le faire lire à la fraiseuse pour qu'elle découper le panneau au dimension souhaitées de manière précise.
- Pouvoir designer les autocollants qui serviront d'écriture sur notre panneau.
- Le logiciel permet de faire facilement des essais de graphique pour tester plusieurs options visuelles.
En effet dans la fabrication de notre panneau, nous sommes passés par plusieurs étapes :
- Le dimensionnement de notre panneau sur une planche en bois contre-plaquée. Nous avons découpé cette même planche avec la fraiseuse pour une découpe très précise.
- Le panneau découpé, nous l'avons peint avec une peinture hydrofuge orange, de la même couleur que celle du Fablab. Cette étape permet de garantir l'étanchéité du panneau pour des conditions d'affichage en extérieur.
- Pour indiquer le Fablab Descartes, nous avons utilisé des autocollants en guise d'écriture. Il a donc fallu qu'on modélise ces écritures avec le logiciel Inskape. La modélisation terminée, nous avons transmis nos données à une découpeuse pour qu'elle forme nos indications sur du papiers autocollants. Le principe de ce papier est simple, c'est un gros autocollants dans lequel il faut découper les formes souhaitées, il faut ensuite les détourées et pour conserver les écarts imaginés à la modélisation, il faut manipuler nos autocollants avec un papiers de transfert. C'est donc ce que nous avons fait pour obtenir notre panneau.
- Enfin pour sécuriser l'ensemble, nous avons vernis le panneau avec les autocollants pour renforcer l'étanchéité.
Impression 3D







Après la validation du modèle 3D, nous avons lancé l'impression des différents composants du boîtier technique. Une imprimante 3D a été utilisée, permettant de transformer nos idées virtuelles en éléments physiques concrets. Cette étape a confirmé la faisabilité de notre projet et a permis de détecter d'éventuels ajustements à apporter.
L'impression des composants s'est avérée chronophage, avec un temps total d'impression dépassant 36 heures pour l'ensemble des pièces.
Le résultat final a répondu à nos attentes, les pièces imprimées sont sorties avec les dimensions et les formes initialement conçues. Elle a également facilité les étapes ultérieures d'assemblage et de finition.
La première étape après l'impression consistait à éliminer les supports d'impression, nécessaires au maintien des pièces pendant l'impression. Le ponçage des surfaces a permis d'obtenir un fini lisse et uniforme, améliorant l'aspect esthétique des pièces. Cette étape a contribué à valoriser le produit final et à garantir sa qualité.
L'impression 3D et les ajustements après impression des boîtiers techniques ont permis de concrétiser la conception et de produire un prototype fonctionnel et esthétiquement abouti.
Le type de plastique utilisé pour l'impression de nos pièces est du PETG. Nous le recommandons dans la mesure ou il est économique. En revanche des micro trous peuvent apparaître à l'impression ce qui peut mettre en péril l'étanchéité des boîtiers.
Aussi voici les imprimantes utilisées pour l'impressions de nos pièces.
Assemblage Des Composantes





Dans notre projet, nous avons du assembler un ensemble de pièces pour mener à bien le projet. On procède comme pour un assemblage de poupées russes inversé : nous commençons par emboîter les plus petites pièces ensemble pour finir par le grand panneau. Les pièces à assembler sont : Couvercle - Boîtier/ Porte-Boîtier/ Boîtier- Panneau/ Panneau - Poteau.
Pour simplifier la compréhension nous détaillerons en image, notre projet lors de l'assemblage.
Des retouches ont été nécessaires pour garantir un emboîtement parfait des pièces et un fonctionnement fluide des mécanismes. Nous avons du limer les rails pour glisser les portes, dégager les résidus de plastiques pouvant bloquer l'insertion des visses de 3mm pour attacher le couvercle technique au reste de l'ensemble.
Chaque composant trouve sa place naturellement dans les compartiments conçus à cet effet : la carte Arduino et son shield de relais s'emboîtent parfaitement, les câbles électriques s'organisent dans leurs espaces appropriés.
- Emboîtement de la carte Arduino et du shield de relais dans le boitier technique majeur
- Organisation des câbles dans les guides intégrés
- Fixation des couvercles technique avec des vis de 3mm
- Glissement des portes pour fermer les boîtiers
La fixation du boîtier sur le panneau en bois a été particulièrement soignée. Nous avons utilisé des vis qui maintiennent l'ensemble tout en permettant un démontage aisé pour maintenance. De même pour fixer le panneau au poteau, nous l'avons visé et l'ensemble a très bine tenu.
Aussi sur la dernière photo, nous avons fait face à un problème d'étanchéité sur le boitier majeur, pour cela nous avons positionné un sac plastique pour récupérer l'eau. Ce problème est apparu lors de l'impression du boîtier à l'imprimante 3D.
Tests





Enfin une fois la conception terminée, la modélisation effectuée et l'impression achevée respectivement nous avons tester le code Arduino avec les brumisateurs, nous avons tester l'étanchéité des matériaux imprimés...
Cette étape est cruciale et permet de toujours remettre en cause nos idées, le projet... Cette étape permet aussi de nous remettre personnellement en question. Faire face à un problème nous stimule dans la recherche de solutions, d'alternatives, de plans B... C'est aussi un moment tendu qui peut provoquer du stress, du challenge. La dopamine est alors à son maximum.
Les différents tests que nous avons effectués :
- Les brumisateurs programmés, mis en milieu aqueux (consommation en eau, bon fonctionnement...)
- Batterie raccordée, comme sources d'alimentation
- Test des flotteurs
- L'étanchéité des réservoirs
Les brumisateurs
Nous les avons testé en téléchargeant le code ci-joint plus haut. Nous devions savoir qu'elle quantité d'eau ils consommaient ensemble. Cette donnée nous a été utile pour dimensionner nos réservoirs pour garantir une capacité suffisante d'eau au bon fonctionnement du panneau. Conso/heure : 1,6 cl/h pour 2 brumisateurs.
Les tests ont été validé et nous avons pu procéder à la suite de notre projet.
Batterie
Nous devions savoir si notre système fonctionnait de manière autonome, alors se faire nous avons opter pour une batterie portable, rechargeable à l'énergie solaire. Alors au lieu de brancher les composants Arduino, les brumisateurs... sur une prise classique USB, nous devions tester si la batterie était assez puissante pour alimenter notre système.
Le test à été validé et nous avons pu procéder à la suite de notre projet.
Les flotteurs (c'est la pièce qu'on voit en plus du brumisateur)
Ils servaient à caler les brumisateurs, les maintenir à flot pour leurs permettre de bien fonctionner. En effet, s'ils sont immergés, le fonctionnement est remis en cause, la fumée ne sors pas. Alors il était important de trouver un moyen de les positionner à 90° par rapport au niveau de l'eau. Nous avons fait des flotteurs en matériaux de récupération : de la mousse de frite ( objet qu'on retrouve dans les magasins de sports au rayon natation), des bouts d'éponges et de la colle chaude. L'ensemble forme un socle où l'on clipse le brumisateur.
Le résultat est mitigé car en effet le support flotte mais il n'empêche pas à la tête du brumisateur de ne pas être immergée. Il stabilise l'ensemble tout de même mais le système est à perfectionner.
L'étanchéité
Après l'impression de nos réservoirs, nous devions tester leur capacité de rétention d'eau. Sur le réservoir mineur, l'étanchéité se fait bien malgré que de l'eau s'infiltre dans les parois, ce qui n'est pas grave car le PETG résiste à l'eau. En revanche, pour le réservoir majeur il faut trouver un système annexe pour garantir l'étanchéité car en effet, l'eau coule du réservoir de manière abondante et les capacité de stockage sont très limitées.
La solution provisoire est de mettre un sac plastique qui recouvre les parois du réservoirs pour contenir l'eau. Le sac plastique agirai alors comme un liner de piscine.
La Présentation


Après toutes ces étapes nous présentons notre projet de panneau fumant devant un assemblée de personne du département génie urbain de l'université, de Thomas et Antoine du Fablab, des personnes de la MEI et notre classe.
C'est le moment de monter notre projet, de parler des étapes par lesquelles nous sommes passées et les défis relevés et de statuer sur ce qui à plus ou moins marcher, ce qui est à améliorer...
Nous avons utilisés, à l'exception des brumisateurs et des pièces techniques sur mesures, que des matériaux de récupérations et nous voulions vraiment être dans une démarche de réemploi. Nous voulions crée un symbole à travers notre panneau pour que le Fablab Descartes ainsi que tout les Fablabs de France manquant de visibilité bénéficient d'un élément tout de suite identifiable qu'est notre panneau fumant.
C'est un très bon début, il reste des points à améliorer, l'idée principale est là et nous pouvons être fier de notre projet.