Soccer Playing Robots



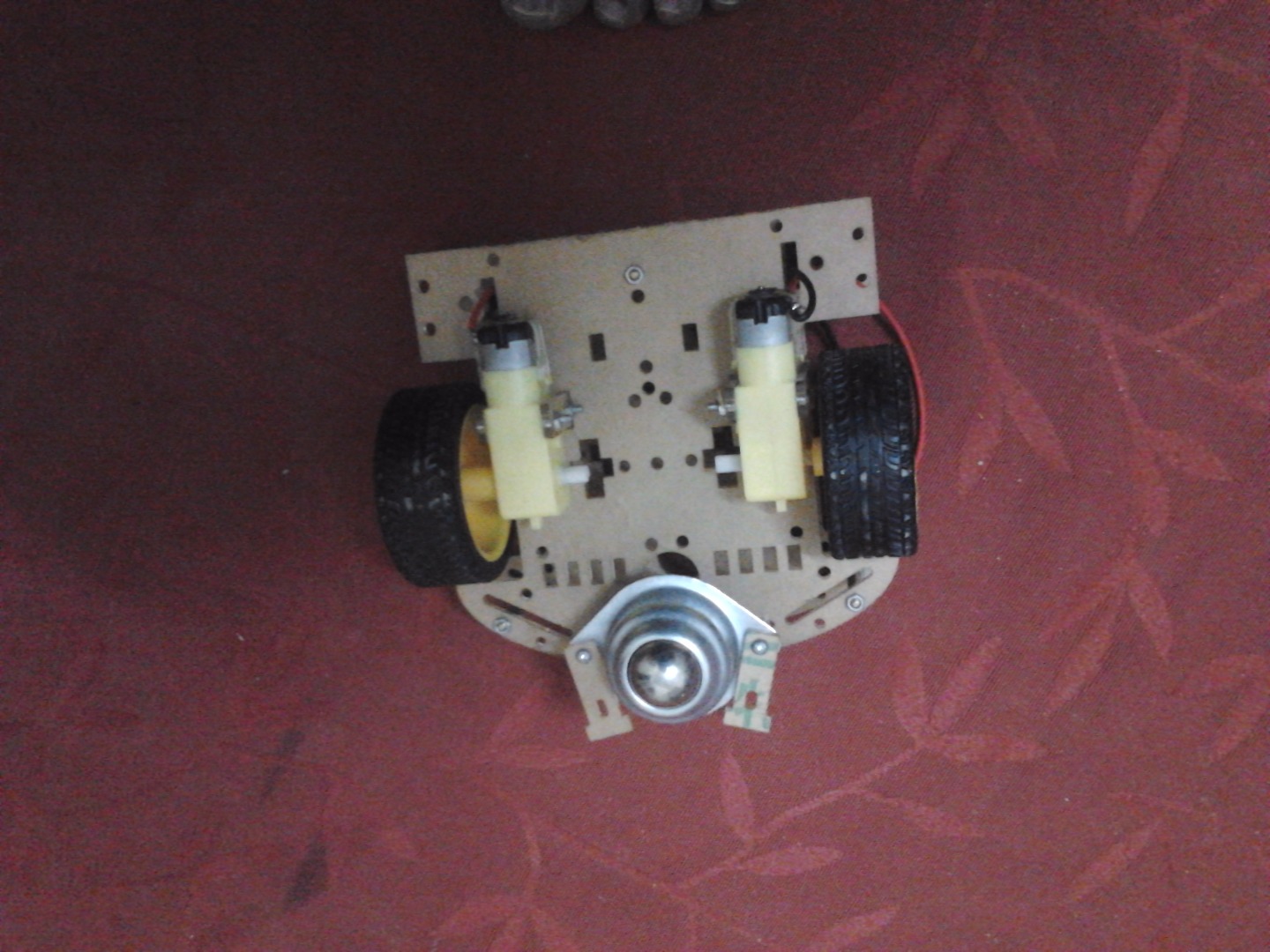

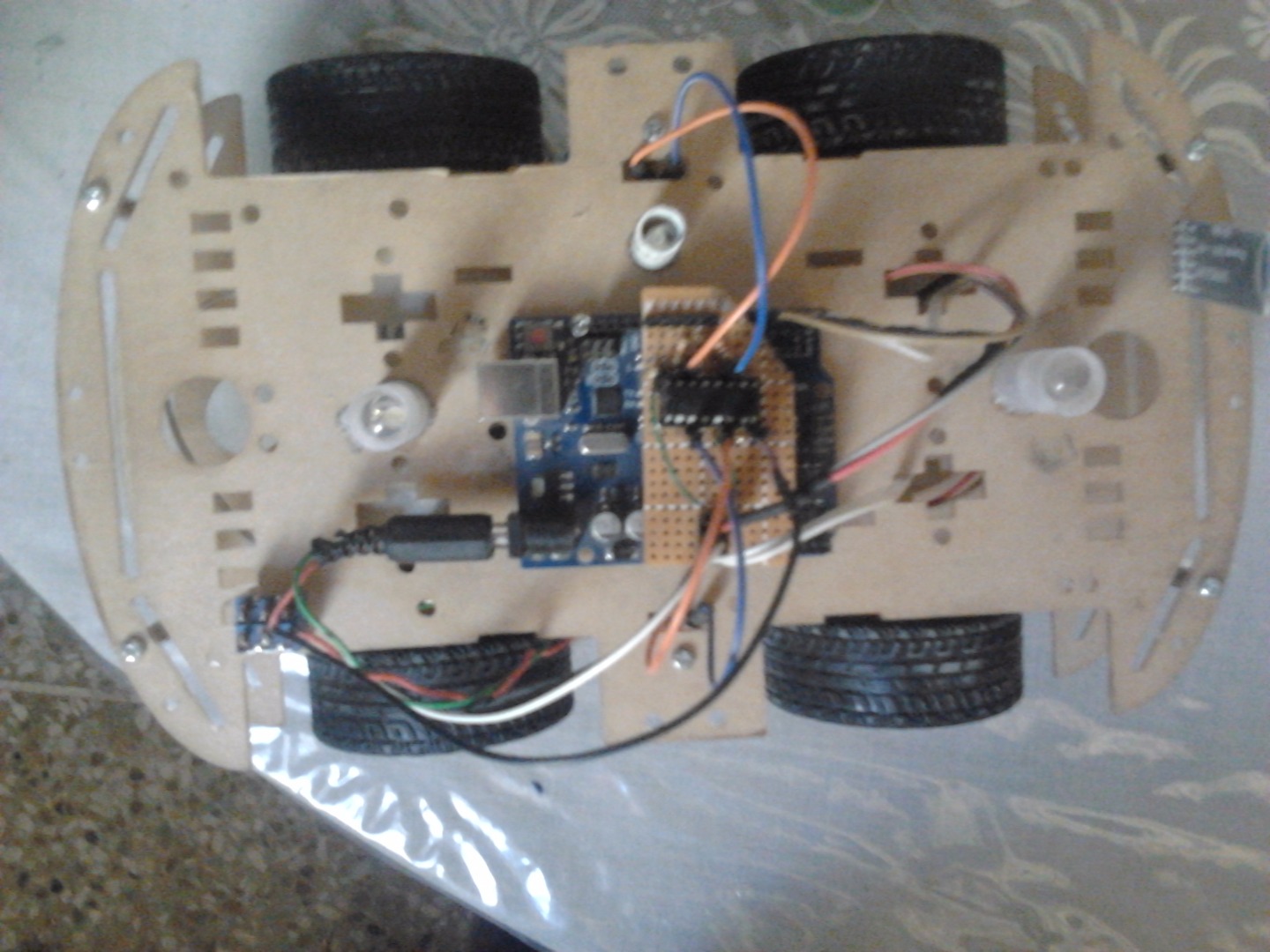




















This is my final year project. The pics and details are too much to re-write so i have attached the pictures and uploaded the report as well. I hope it will help someone :)
The project objective was to make a software based controller to make 2 robots play soccer against each other. Matlab was used for image processing and controller was made in the same software.
The idea was derived from SSL robots. However this project is much simpler.
Downloads

Chapter # 1
Introduction
1.1 Project Overview
Autonomous robots are designed to do certain task on the basis of algorithm embedded in them and they are mostly limited to a described field. These robots need a system to judge their surroundings, their position in that environment, a way to perform the assigned task and how to do that precisely. When multiple robots are present the complication increases greatly as one robot has to be designed intelligent enough to perform the task without effecting the other.
The small size league (SSL) robots are a part of soccer playing robots team. The robots in this team are guided by software in all aspects like their teammates, opponents, position of goals and the ball. Both the teams have exact same hardware as for this competition hardware is standardized. So basically the competition is all about the software designed to control a team. This software consists of all the basics modules required to determine the visual aspects as well as the algorithm to tell a robot what to do and how to do. The main focus of this thesis was on image processing and trajectory tracking. [1] [8]
The main idea is motivated from the SSL robots but the structure is different, like this thesis does not comprise of a team rather, it consists of two opponent robots that will play soccer against each other. The design of robot, its dimension, way of movement and stadium dimensions are also different. The basic steps involved in the operation of project includes capturing of image through a camera then that image is converted to more suitable form that the software can handle like Grayscale image or standard RGB(Image made by the combination of standard colors only image that are red, green, blue). Image processing is done to determine position of the robots and ball. The controller designed gets the appropriate information from the image and determines what the robot should do next to score a goal.
1.2 Problem Description
The small size league (SSL) uses quite complex concepts for soccer playing robots teams and if one wants to make a robot for small size league (SSL) it is very difficult especially for beginners. So this project can serve as a guideline to all the basics concepts that can help to make a SSL robot.
The main idea of this thesis was to make a software based controller that can allow two robots to play soccer against each other using image processing for object tracking and serial interface for communication.
1.3 Project Objectives
· Image processing for orientation and position of robots and ball
· Design a software based controller to make two robots play soccer against each other
1.4 Project Scope
This thesis shows one of the ways to bring automation to a robot by designing a software based controller. As bringing automation to machines is one of the most important aspects of modern technology. This thesis is different in most of the ways from the standards of small sized league robots (SSL). However the algorithm used in this project is same as used in SSL. This project depicts the most basic things and study required to develop robot for SSL and it can serve as a basic guideline to someone who is interested in developing SSL team.
Chapter # 2
Literature Review
2.1 RoboCup Background
RoboCup is a scientific initiative with a sole purpose to increase research and students interest in various technological fields by providing a standard platform like the robot soccer games. The idea behind this concept was to make robots intelligent enough by designing complex controller to have a humanoid robot team that can play against human soccer players under official FIFA rules.
RoboCup has four main interests: RoboCup Soccer, RoboCup Rescue, RoboCup home, and RoboCup Junior. RoboCup Soccer has 5 leagues: Humanoid, Middle Size, Simulation, Small Size, and Standard Platform. The WPI Warriors team first competed in the Standard Platform League in 2011. This league has fixed hardware, so only the software can be changed.
The RoboCup most advanced league uses the Aldebaran Nao robots as shown as shown in Fig 2.1 Project Nao launched in 2004 and the Nao robots have been the robot of the SPL since 2010. The most recent release of the heads for the Nao robots is version 4, which features 2 high-definition cameras (1280x960), an Intel ATOM 1.6 GHz CPU, and wireless communications over Wi-Fi. The body of the robots features 21 degrees of freedom [1]
Figure 2.1: Diagram of Aldebaran Nao [Taken from [1]]
2.2 Small Size League (SSL) RoboCup Framework
One of the categories in RoboCup is SSL i.e. Small size league robots category. It consist of smaller size robots teams. Each team consists of six robots. Hardware of both the teams is exactly same the only thing that is different is the software or the algorithm used to control these robots. Fig 2.2
Figure 2.2: Small size league robot [Taken from [1]]
The camera feed is given to both teams owners. SSL vision software is used to get required information from the real time captured frames. After processing the image the orientation and position information is given to the software based controller. This controller then tells the robots what to do and how to do it. [5]
2.2.1 SSL-Vision
It is the software and hardware setup required to find the ball and robots position and orientation in the field. Previously Small Size League rules allow each team has their own global vision system. The progress made by individual participating teams was pretty close to each other and only minor difference or upgrading were present. Hence the responsible committees decided to migrate to a shared vision system (including also sharing the vision hardware) for all teams by 2010. This system named SSL-Vision is currently developed by volunteers from participating teams. [4]
Other major problems with individual vision setup were that the setup time required before as well as during the competition was too much, as having five teams playing on a field; ten cameras need to be mounted and calibrated. During these preparations, a field cannot be used for any matches or other preparations.
Due to the standardized field size, SSL-Vision becomes an ideal solution for the Humanoid as well as the Standard Platform League.
2.2.2 Framework for SSL-Vision
The figure 2.3 shows an overview of the framework architecture. The entire system's desired processing flow is encoded in a multi-camera stack which fully defines how many cameras are used for capturing, and what particular processing should be performed. The system has been designed so that developers can create different stacks for different robotics application scenarios. By default, the system will load a particular multi-camera stack, labeled as “RoboCup Small Size Dual Camera Stack”.[3]
The software includes all the stuff from camera calibration to the pattern recognition for individual robots of each team. And updates the information provided to each team on real time basis.
The real-time progress is achieved by using plug-in to interconnect the software with a good video card. Currently SSL-vision uses Nvidia Geforce 7800GTX videos card.
Figure 2.3: Small size league robot [Taken from [3]]
The SSL-vision uses extended Kalman filter for localization purposes. Robot localizations is quite difficult task when the field of view is limited and with limiting processing capabilities. The two most commonly used strategies for this purpose are Kalman filtering and particle filtering.
2.3 MATLAB
MATLAB is commercial "Matrix Laboratory" software that provides a user friendly environment for interactive programming. MATLAB provides a vast variety of built-in functions including almost all of the mathematical expressions and visualization like graphs and image processing. MATLAB provides matrix computations, signal processing, numerical analysis and graphical environment with easy built-in functions and thus reduces the requirement of traditional programming. [6]
In my thesis MATLAB is used basically for image processing and controller designing. MATLAB gives all the image processing features like image enhancement(sharpening or un-blurring an out of focus image, highlighting edges, improving image contrast, or brightening an image, removing noise), image restoration (removing of blur caused by linear motion, removal of optical distortions) and image segmentation (finding lines, circles, or particular shapes in an image, in an aerial photograph, identifying cars, trees, buildings, or roads etc.)
2.4 Trajectory Tracking
Tracking means following a defined path. For different wheel vehicles different equations are derived to make them follow the path keeping in mind the slippage of wheels and precision of movement. For unicycle type robot with two actuated wheels on a common axle and a midpoint “M" between the two wheels the equations is as follows
[2]
Here v and w are the robot translation and angular velocity of the robot respectively and the theta denotes the vehicle's angle in the field with respect to a fixed co-ordinate system.
2.4.1 Control of a unicycle type robot
The equation of the controller for the unicycle-type robot in the “Trajectory tracking for unicycle-type and two-steering-wheels mobile robots” by “Alain Mi-caelli and Claude Samson” [2]
[2]
The following are the results of the controller formed for two reference trajectories Fig 2.4 is a straight line trajectory tracking result of a robot and Fig 2.5 is of a semi-circle trajectory simulation result.
Figure 2.4: Results of a robot following straight line trajectory [Taken from [2]]
Figure 2.5: Results of a robot following semi-circle trajectory [Taken from [2]]
The deviation in these results is due to the slippage of wheels and the minute difference between the rpm of the two driving wheel motors as two motors cannot be hundred percent identical.
Chapter # 3
Requirement Specifications
3.1 - Functional requirements
3.1.1 – Capture from webcam
The software will interact with the webcam attached and capture a frame,
3.1.2 – Process the captured frame
Once the frame is captured it will be processed in the following way
3.1.3 – Conversion to binary image
The captured frame is converted into binary frame for easy processing and reducing the load on the system.
3.1.4 – Calculate frame dimensions
The captured frame’s dimensions are acquired for calibration.
3.1.5 – Calculate Region of interests (ROI)
Once the frame is ready and filtered the regions of interest are extracted that are basically the detected objects on the stadium field.
3.1.6 – Arranging the Region of interests (ROI)
The detected regions are then arranged according to their respective sizes so they can be sequenced and respective information can be acquired. Each object size represents a specific ROI like the biggest detected ROI is for the goal position.
3.1.7 – Comparing the findings
The controller then looks for the conditions of movement. Like it compare the angle between the robot and the ball. If the angle is greater or less then certain amount the robot rotates to face the ball.
3.1.8- Sending the commands
After the conditions are checked, if the condition is not satisfied like the robot is facing not towards the ball the controller will send rotation command to rotate the robot so that it faces the ball. On the other hand if the condition is satisfied the controller checks for the next condition.
3.2 - Non functional requirements/Quality Requirements
3.2.1 Speed
The software controller and the image processing algorithm is fast and can process four frames per second and it can perform better if a better computer is used.
3.2.2 Efficiency
The motion of the robots is precise and accurate by reducing the slippage and better design model.
3.2.3 Reliability
The project is reliable and secure as each wireless communicating modules is secured by a unique password. Proper circuits are designed and components are selected after doing calculation so that nothing is loaded then more it can handle.
3.2.4 Legal and licensing
The software base controller has no legal or licensing issues, as I am using open source software like Arduino 1.0.5 and MATLAB 2014a.
Chapter # 4
System Design
4.1 Design Methodology
The Fig 4.1 is the methodology on which the project operates
Figure 4.1: Methodology of the project
For vision a web-cam is used to acquire frames. Image processing is done on MATLAB. From the processed image information like the position of goals, ball and angle and position of robot is determined. The information acquired then is used to feed the controller for motion of the robot.
4.1.1 Vision
A webcam is selected to get the live streaming of the stadium field. The reason for selecting a webcam is that the image quality is good enough to get the information from the frames being captured and small resolution reduces the processing load as well.
4.1.2 Image processing
Each captured frame is processed. The processing includes the conversion to binary images, splitting the frame into channels to get better results. Each captured frame has slight variation of threshold of the detected objects for the red, green and blue channel. Once the objects are detected in each channel the channels are merged together to get the region that is common in all.
4.1.3 Localization
The detected objects are then labeled and their values like the area they occupy and centre points are stored in matrices so they can be used by the controller.
4.1.4 Controller
Each robot has its own software based controller that is programmed in MATLAB software.
The controller’s main job is to check for the conditions and decide what it should do next to make robot approach the ball and score the goal. Or in the other case it if the other robot is trying to score a goal how can it stop it.
4.1.5 Behavior
After the controller checks for conditions and decides what to do it send motion commands to the robots and the robot’s job is to act on the commands being send. Including moving forward, backward and rotation in either directions.
Chapter # 5
System Implementation
To implement the project it’s been categorized in the following three main parts.
o Vision system
o Controller
o Robots
5.1 Vision System
The diagram 5.1 shows the data flow of the vision system
Figure 5.1: Vision system components
5.1.1 Camera
I am using Lenovo q350 USB web-cam for image capturing. It has resolution of 320x240.The smaller resolution makes the image less detailed hence the image processing can be done at a better speed. It has a USB interface and is compatible with every operating system.
Resolution
320x240
Operating voltage
4V-6V
Capturing speed
25 fps
Table 5.1: Camera Specifitaions
5.1.2 Computer
Computer is used for image processing and data communication between robot and the software based controller. Any computer can be used preferably with 1GB of RAM and a dual core processor as image processing requires resources like RAM and Video memory. More memory helps in having a bigger buffer that can help in speeding up the image processing process after capturing the frames from the attached camera.
Processor
Core 2 Duo E8400
RAM
2 GB
Chip-set
Intel G41 series
Table 5.2: Specifications of computer used for thesis
5.1.3 MATLAB
MATLAB is used for image processing and designing the controller for the robot motion. MATLAB Image acquisition tool is used to link the camera with the MATLAB software. This tool has built-in functions for processing an image and acquiring required information from either an image or an array of images or even live stream.
In this thesis I used MATLAB for tracking the objects. In my case there are two robots, ball and two goals which are the main objects to be tracked. Ball tracking just requires position but for a robot its angle is as important as its position. Without angle a robot cannot be moved to a desired location, the object will not be in front of it all the time so it had to move on certain angle so that it faces its target and then move straight towards the target. As displacement is the shortest path to the target. For tracking an object in real time streaming, each frame is processed individually to get region of interest. The acquired frame is then broken down into RGB channels. From these channels the region of interest is obtained by subtraction or using logical operations like "OR" operation and "AND" operation. Dividing the frame into channels helps in getting more precise results as different channel have a little different threshold of different colors. [7] [9]
After the region of interest is highlighted in each channel they are joined together by "AND" operation to get the common region in all of the respective channels. Filtering can be done after this step to avoid noise. The frame is converted into binary for blob analysis. Blob analysis gives the region in a binary image that has different properties with respect to other image like a white spot on a black colored area. Blob analysis in MATLAB also provides several functions like bounding box (Draws a box around the region of interest in an image), Centroid (Gives the center point of the region of interest in an image), Labeling (to label the region of interest in an image) and blob count (number of regions of interest in an image). After the frame's information has been extracted it is given to the controller that decides what should be done next for robots motion. All these steps are repeated for individual frames that are acquired from the camera. [8]
The controllers main job is to direct the robot towards the balls. The secondary objectives of controller are to avoid collisions, direct the robot to hit ball in the direction of the goal and take the shortest path to reach the ball. The controller designed uses computer's serial port to send the data via USB Bluetooth to the robot.
5.1.4 Bluetooth Transceiver
After the image is processed and required information is given to the controller, it generates an output to be sent to the robot for movement. Different communication modules can be used here like Radio transceivers, IR transceivers and Bluetooth transceivers. I am using Bluetooth transceivers for their simplicity and lower power consumption as compared to the other two modules. Bluetooth transceivers are plug and play devices so easy to install and are ideal for smaller distances. The device I used is 2.0 Bluetooth USB dongle.
Interface
USB 2.0
Support system
Windows 98/98SE/ME/2000/XP/Vista
Symbol rate
Symbol rate
Receiving and sending range
Up to 20 m
Support Bluetooth
V 2.0 and V 1.2
Table 5.3: Specification of USB Bluetooth module
5.2 Controller
The controller checks for several conditions before sending a movement command to the robot.
5.2.1 Checking for ball position
The controller first job is to heck for the ball position that whether it lies in front of it or behind it. If it lies behind it the robot alligins it self with x axis and starts reversing until the ball is in front of it. If its already in fron the controller jumps to the angle comparison algorithm.
5.2.2 Angle Comparison
Instead of trying to approach ball the robot tries to get to a point that is at a specific distance behind the ball. It first faces the ball by comparing the angle between ball and robot’s head to ball and robot’s base. If that difference is greater then +_ 5 degrees it rotates the robot left or right to face that imaginary point. Once it faces that point it starts moving towards it.
5.2.3 Hitting the ball
After reaching the imaginary point the controller alligns the robot in direction of goal and hit the ball in direction of goal with some momentum. The figure 4.2 shows the imaginary point placement. The point ‘G’ represents the postion of goal on the stadium, the point ‘B’ represents the current position of ball and ‘I’ represents the imaginary poit defined by the controller.
Figure 5.2: Imaginary point placement
5.2.4 Defending
The controller also checks for the condition like if one robot is too close to the ball its obvious that it will reach the ball first. So instead of trying to approach it the controller makes the robot defend the goal by making robot come in between ball and goal.
5.3 Robot
The figure 5.3 shows the data flow in the robot
Figure 5.3: Components of robot
5.3.1 Bluetooth Transceiver
The robot uses HC-05 module for getting instruction from the software based controller present in the computer. HC-05 is the most widely used transceiver having both master and salve configuration options. The module has built-in memory for information storage and provides a number of configuration options. The options include changing of module display name, password, master slave configuration and baud rate settings. [14]
Mini Size(L x W x H)
Approx. 27 x 13 x 2mm
Operating Frequency Band
2.4GHz
Bluetooth Specification
V2.0+EDR
Output Power Class
Output Power Class
Operating Voltage
3.3V
Flash Memory Size
8Mbit Storage
Temperature
−40◦C to 80◦C
Working Temperature
−25◦C to 75◦C
Table 5.4: Specification of HC-05 Bluetooth module
5.3.2 Arduino UNO R3 (Microcontroller)
In this project the micro-controller is used as a medium for converting the bits received from Bluetooth module of robot into information that a motor driver IC can understand. Arduino UNO R3 uses ATmega328 micro-controller that is ideal for a scenario like this project with enough speed and error free translation. [15]
Micro-controller
ATmega328
Operating Voltage
5V
Input Voltage(recommended)
7V-12V
Input Voltage(limits)
6V-20V
Digital I/O Pins
14 (6 provide PWM output)
Analog Input Pins
6
DC Current per I/O Pin
40 mA
DC Current for 3.3V Pin
DC Current for 3.3V Pin
Flash Memory
32 KB 0.5 KB used by boot loader
SRAM
2 KB
EEPROM
1 KB
Clock Speed
16 MHz
Length
68.6 mm
Width
53.4 mm
Weight
25 g
Table 5.5: Specification of Arduino UNO R3 micro-controller
5.3.3 Motor Driver IC
L293D is a dual H-bridge IC used for controlling DC motors. Dual H-bridge makes it capable to control two DC motors simultaneously. Smaller size, low power consumption for IC operation i.e. 0.120 watt, less heat and separate rails for IC operation and motor driving make it ideal for small size robots
Product
DC Motor Controllers / Drivers
Type
H-Bridge
Operating Supply Voltage
4.5V to 36V
Output Current
600 mA
Operating Temperature
−40◦C to +150◦C
Supply Current
2 mA
Mounting Style
Through Holes
Package/Case
PowerDIP-16
Number of Outputs
2
Table 5.6: Specification of L293D motor driver IC
5.3.4 Motors
The robot uses 4 DC brushed motors for movement. Each motor has a gearbox for better torque and lower speed. Lower speed gives precise movement in the stadium field and high torque reduces motor load as the robot weighs 2 kg. The motors are used in pairs for movement. If right pair of motors turn clockwise and left pair of motors turns anti clockwise the robot turns left, similarly if right pair of motors turn anti clockwise and left pair of motors turns clockwise the robot turns right. To move forward both pair of motors turn clockwise and anticlockwise for backward motion respectively. All this motion control is achieved by the motor driver IC.
Operating Temperature
−10◦C to −60◦C
Rated Voltage
6.0VDC to 12.0VDC
Rated Load
10 g*cm
No-load Current
70 mA max
No-load Speed
Speed 9100 +-1800 rpm
Loaded Current
250 mA max
Loaded Speed
4500 +-1500 rpm
Starting Torque
20 g*cm
Starting Voltage
2 VDC
Stall Current
500 mA max
Max Body Size
27.5 mm x 20 mm x 15 mm
Shaft Size
8 mm x 2 mm
Table 5.7: Specification of DC motors used in robots
5.3.5 Security
The robots communicate with the computer by the Bluetooth modules. Their default passwords are ‘1234’ so if anyone knows the default passwords he can connect with the robots. So the default passwords of both of the module present on the robots have been changed to avoid misuse.
Chapter # 6
System Testing and Evaluation
6.1 Graphical user interface testing
As this project is not a prototype of something that has to be presented in the market, it doesn’t have a GUI made for the software. The sole purpose of this project was to implement what was learnt during the bachelor degree program and to learn more about semi-autonomous robotics and image processing.
6.2 Usability testing
Although the software lacks graphical user interface its quite simple to use. The user will require MATLAB version 2014a and the “m” file built for this project having the vision system and the controller. So the person who wants to see working of this project just needs to have the basic knowledge about the MATLAB software.
The hardware part is even simpler as the user just need to switch the power button present on the robots.
6.3 Software performance testing
MATLAB is not made specifically for image processing although the image processing tool in MATLAB has almost all the functions required to process an image and acquire useful information from the captured image. Image processing in MATLAB is not as fast as it can be in software solely made for this purpose. Keeping this thing in mind still the controller loop takes only 0.5seconds to 0.8 seconds to process a single frame that is adequate. As the knowledge about image processing was in learning phase so still there might be couple of things that can make the software performance even better.
6.4 Compatibility testing
As far as compatibility is concerned it all depends upon the system the software is being run at. The system use for testing of the project was having a dual core processor and 2GB or RAM. So if the system is faster the software will perform better and if it’s slower the performance of the software will decrease also.
In hardware the robots require quality batteries and having voltage level above 8v. Although the Arduino can work on lower voltages fine but as the batteries fail to provide enough power to run the motors and do serial communication at same time, the connection of the Bluetooth modules drop. So 8V to 12V batteries are recommend that are charged above 20 percent for flawless operation of the project.
6.5 Exception handling
The default baud rate of the hc-05 and hc-06 devices is 9600 bits per second; it’s enough if the data send serially is at regular intervals or requires fewer rates. For my project the commands from the controller are not sent at exact same interval as some frames require less time in processing and some require more. So the default baud rate was resulting in connection drop. To overcome this problem default baud rate were set to 115200bits per second and to change the default security pins of the Bluetooth modules they were modified.
The speed of the robots’ motion was also improved by sending twice motion command per frame processed instead of sending a single motion command.
6.6 Hardware testing
The motor driver IC L-293D can handle a maximum current of 650mA per channel with 2 300mA current rated brushed motors attached to each channel the current reaches 600mA. Although it lies within specs but it is quite close to maximum limits and heats the IC L-293D.
6.7 Security testing
The only components that require security are the Bluetooth modules. This is the reason that their default security pins were changed. But still if someone knows the key then during the operation of the project the robots will be unlinked from the computer and connect to the device that attempted for the connection known as paring in case of Bluetooth devices.
6.8 Limitations
During operation of project no white or red colored objects should be placed on the stadium field. The extra objects detected will slow down the image processing process and that object might be considered as part of the robots, ball or the goal position resulting in false movements of robots.
The robots battery should be charged above 20% to avoid connection drop during operation between paired Bluetooth modules.
The robots cannot hit the ball if it’s lying too close to the stadium borders as in that case the imaginary point defined by the controller might be lying outside the stadium. So the ball should be moved in manually.
Chapter # 7
Conclusion
7.1 Knowledge acquired by work done in this project
7.1.1 Image processing
Image processing proves to be useful in many ways like detecting objects, comparing objects sizes and getting almost all the information about an object including its size, pixels, centre point, color, length etc. Moreover with even a low cost webcam the results of image processing are quite acceptable and accurate so it’s an in expensive yet very powerful tool to have.
7.1.2 Wireless communication between machines
Wireless communication on the other hand is little expensive if used for short distances. But for machine like a robot that has to rotate and move back and forth it the best way of communication as it cannot be done using wires. The distance to what two wireless modules can communicate depends on its quality and quality is directly proportional to cost. I learnt how to do serial wireless communication and also about how much important is the security of wireless communication.
7.2 Improvements
Following are the things that can improve the outcome of the soccer playing robots.
· The wireless range of communication between computer and robots can be improved if high quality Bluetooth modules are used or radio communication can be done in case of big soccer field.
· More robots can be added to make the game more interesting.
· Brushless motors can be used in robots for reliability.
· Algorithm used for vision system as well as controller may be improved for better performance