Waterproof Paper, an Experiment in Making More Useful Materials at Home.
by Natey-Potatey in Workshop > Science
360 Views, 6 Favorites, 0 Comments
Waterproof Paper, an Experiment in Making More Useful Materials at Home.

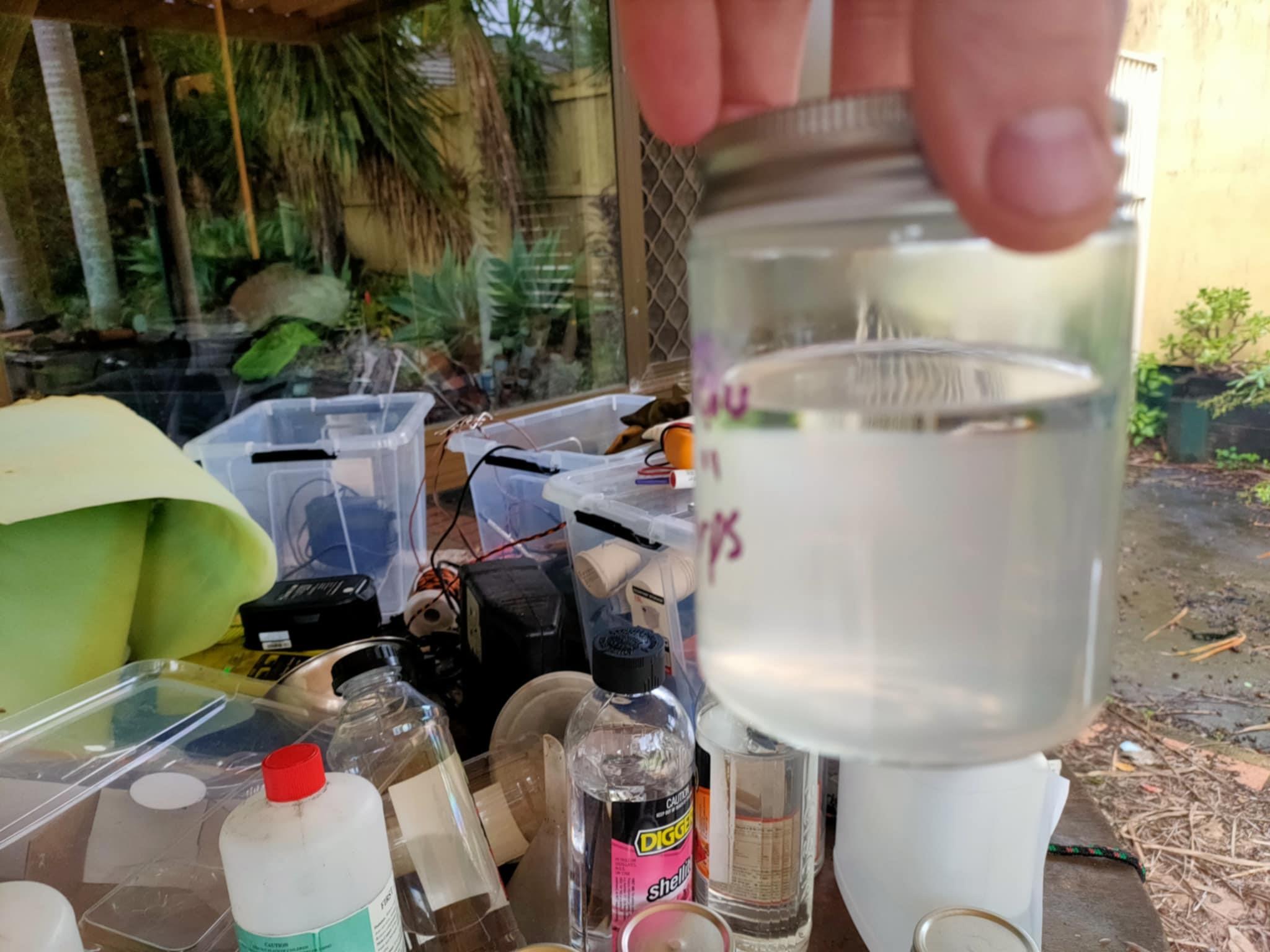

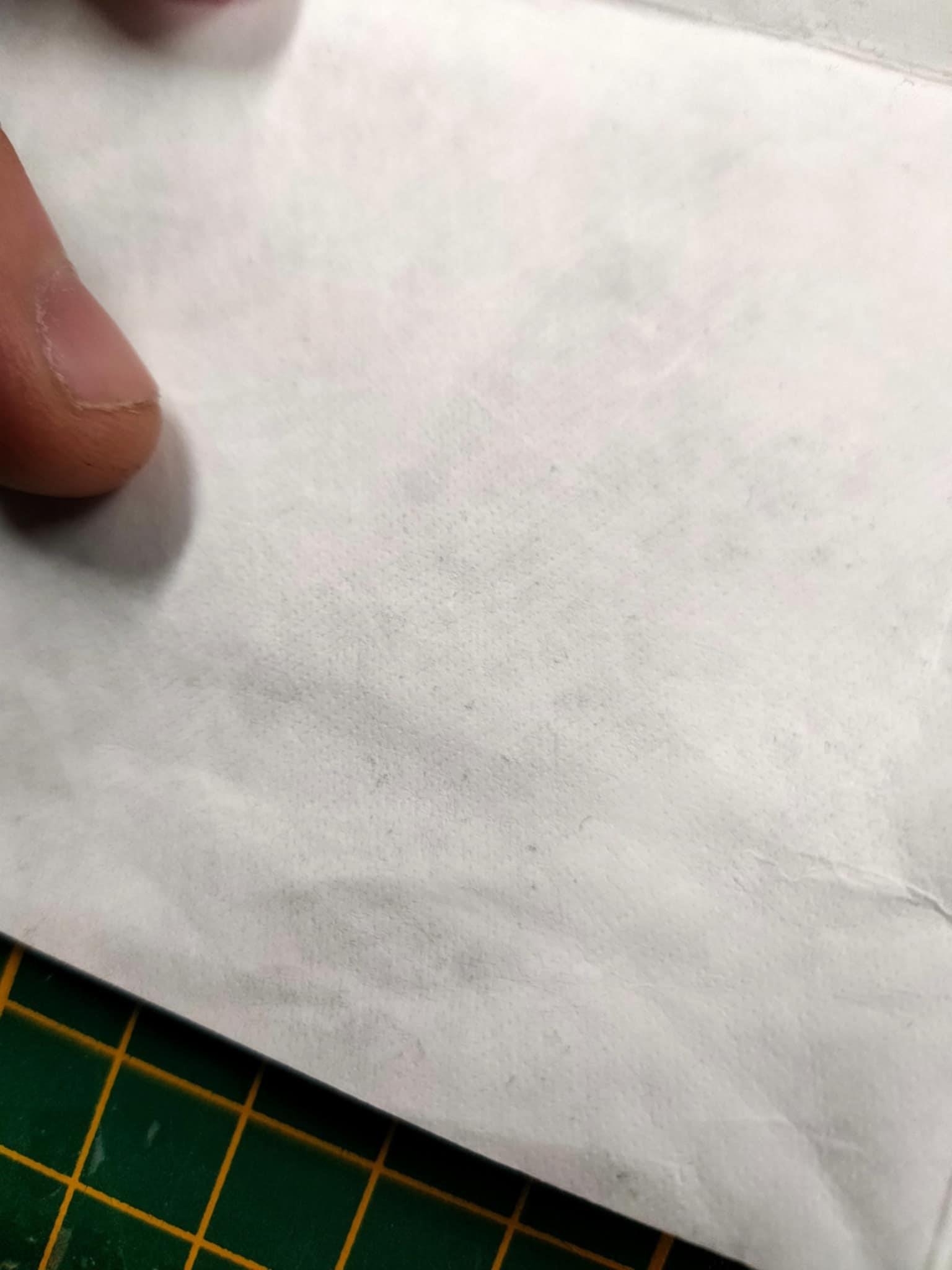

This is a quick report on an "in the shed" attempt to make a material that has some of the useful properties of Tyvek. Tyvek is an industrially made paper-like product made by DuPont, it is lightweight, flexible, and resistant to tearing and moisture. It is often used for "paper wallets", but is also very popular with hiking and camping enthusiasts because of its weight and waterproof nature.
We know we can use polymer layers to provide water resistance and resistance to tearing (contact paper, packing tape, laminators etc), but these put a significant layer of plastic on the paper. This changes both the weight of the paper, and it's ability to be folded or manipulated. I'm also rather useless at smoothly installing contact paper, which means I am likely to ruin any designed items before I can use them in projects.
So to try and recreate the properties of Tyvek, I've attempted to modify an old waterproofing technique used for fabric. In this method silicone caulking is diluted in a solvent and applied to fabric, to impregnate the fibres and waterproof the fabric. This is useful for outdoor wear, or making your own waterproof tarps from fabric or old bedsheets.
While I wasn't able to replicate all the properties of Tyvek for at home use, I did discover a way to make paper waterproof, while still being light, flexible, and useable for some of the purposes paper is useful for.
Supplies





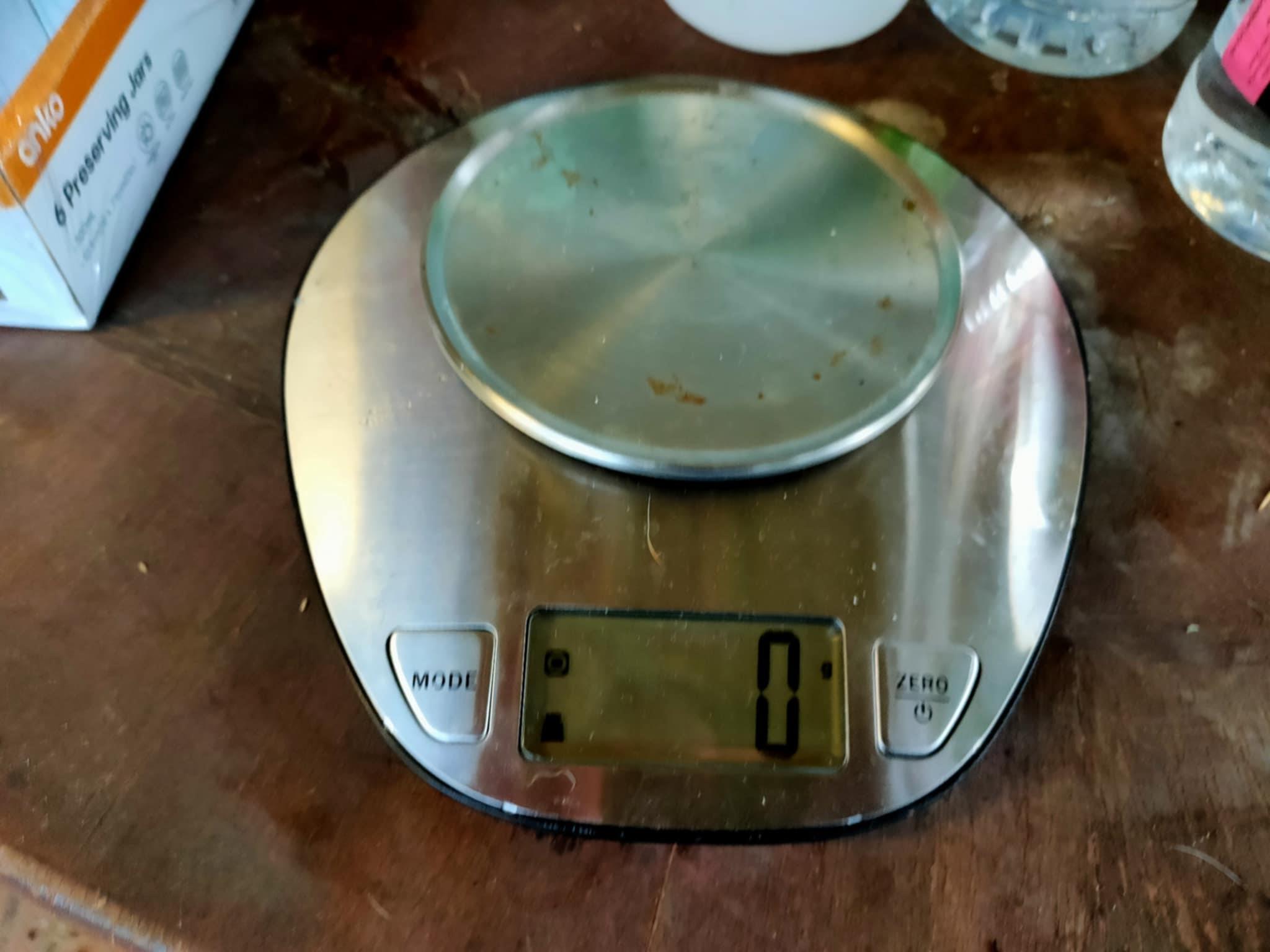


So the original recipe called for silicone caulking, and either Naptha or turpentine. The solvent would normally be mixed at a ratio of 3:1, solvent to silicone, and then painted or soaked into the fibres of the fabric.
In order to coat or impregnate the paper, I wanted to be able to dilute the silicone much more than I'd seen in the forums for fabric. Ideally, if this works, I'd want to spray coat the paper for a consistent coating thickness, but that will be down the line if these experiments are successful.
To get started, I gathered clear exterior silicone caulking, jars for mixing, scales for measuring, and 6 different solvents to trial dissolving/diluting the uncured silicone in. These were Shellite (and Australian product that consists of a naptha fraction), mineral turpentine, methylated spirits (essentially high concentration ethanol with impurities), acetone, Ethylene Acetate and Methyl Ethyl Ketone (MEK). Most of these can be purchased at any trade supply store (I went to Bunnings, which is "Hammerbarn" for any internationals who get their Australian references through Bluey). The Ethylene Acetate and MEK I had left from another ongoing experiment about smoothing PLA prints.
While silicone caulking is available in many colours, I made special effort to get "Clear" silicone caulk so that any discolouration during the process could be identified.
Finally, I made sure to wear gloves whenever handling solvents or uncured silicone, because safety first!
Gather Your Supplies, Weigh Everything and Take Notes for Consistency.



So to begin I took 6 new identical jars (thank you Kmart) and labelled them with the 6 different solvents. To each jar I added 20g of the uncured silicone, and 75 of each of the solvents. The jars were then sealed and shaken vigorously until as much of the silicone was dissolved as possible. The jars were left to sit outside overnight, but were shaken vigorously every hour or so for the first few hours or so.
The next morning, most of the jars still had undissolved silicone in them, so a further 50g of each solvent was added to their correct jars and shaken vigorously again, and allowed to stand for 24 hours. By the time I attempted to use the solvents, it had been at least 36 hours since I initially mixed the silicone and solvent, and had an overall ratio of 125g solvent : 20g silicone, or just over 6:1.
Time to "paint"






When I had time to apply the trial waterproofing agents to paper, I gathered them all up for inspection. Of the 6, 3 seemed to have dissolved or suspended the silicone in solution. These were the mineral turpentine, the shellite (naptha analogue) and the ethylene acetate. Both the acetone and methylated spirits had visibly separated layers of silicone and solvent, and the MEK had a off-colour suspension through the solvent, though there was no visible separation.
The next step, (which I forgot to photograph prior to application) was to tape an A4 sheet of ruled paper to 6 separate cut masonite boards. The masonite has a smooth side, which was useful for keeping the sheets flat while applying the solvent. Each paper was labelled with the name of the solvent mix being tested on it.
Each jar was shaken vigorously, to mix any separate layers in each mix, before a layer of the solvent was applied with a paintbrush to the paper. They were then allowed to dry, and a second layer applied, before being left overnight to fully cure.
The shellite, turpentine, MEK and ethylene acetate mixtures all painted on smooth. The shellite and ethylene acetate dried almost instantly, while the turpentine stayed "wet" for the longest period of any of the solvents.
The acetone mix had visible clumps of silicone suspended in the mixture during painting, which couldn't be spread smooth with the paintbrush. The methylated spirits had even larger, pre-cured clumps in the mixture which didn't adhere visibly to the paper as well.
Check Your Results






So the following morning, I was left with 6 sheets of "waterproofed" paper. A visual inspection showed the following:
Shellite: The coated section of the paper was smooth to the touch, but had discoloured slightly yellow.
Turpentine: This pad had fallen off the table and picked up dirt from the floor, so I am not 100% sure the discolouration was due to the solvent or whether it picked it up from the environment. The turpentine covered layer seemed a little thicker than the other solvents, visually.
Acetone: This solvent was probably the least discoloured of the 6 available, and had the smooth waxy feel of the silicone. However the surface was covered with tiny clumps of silicone, rather than smoothly transfered across the whole surface.
MEK: This was fairly discoloured, even compared to the other samples. The layer of silicone deposited was darker, but still very smooth and evenly distributed across the surface.
Methylated Spirits: The paper itself was not very discoloured where it was fully dry, but there were large, visible clumps of reacted silicone loose on the surface of the paper. These were adhered well enough to not fall off when the paper was lifted, but could be brushed off with hands when handling the paper. Some evidence of a glossy surface, but not enough to be confident in its wateproofing.
Ethylene Acetate: This proved to be a bit of a dark horse among the solvents, as it seemed the least discoloured (other than acetone) of the 6 solvents. It also had a very fine, even coating of silicone on the surface of the paper.
Overall, aesthetically I would rank ethylene acetate as the best candidate, so far. The others either discoloured the paper, or left visible clumping of the silicone on the surface of the paper. The next test will be how water repelling each of the samples is.
Is It Waterproof?
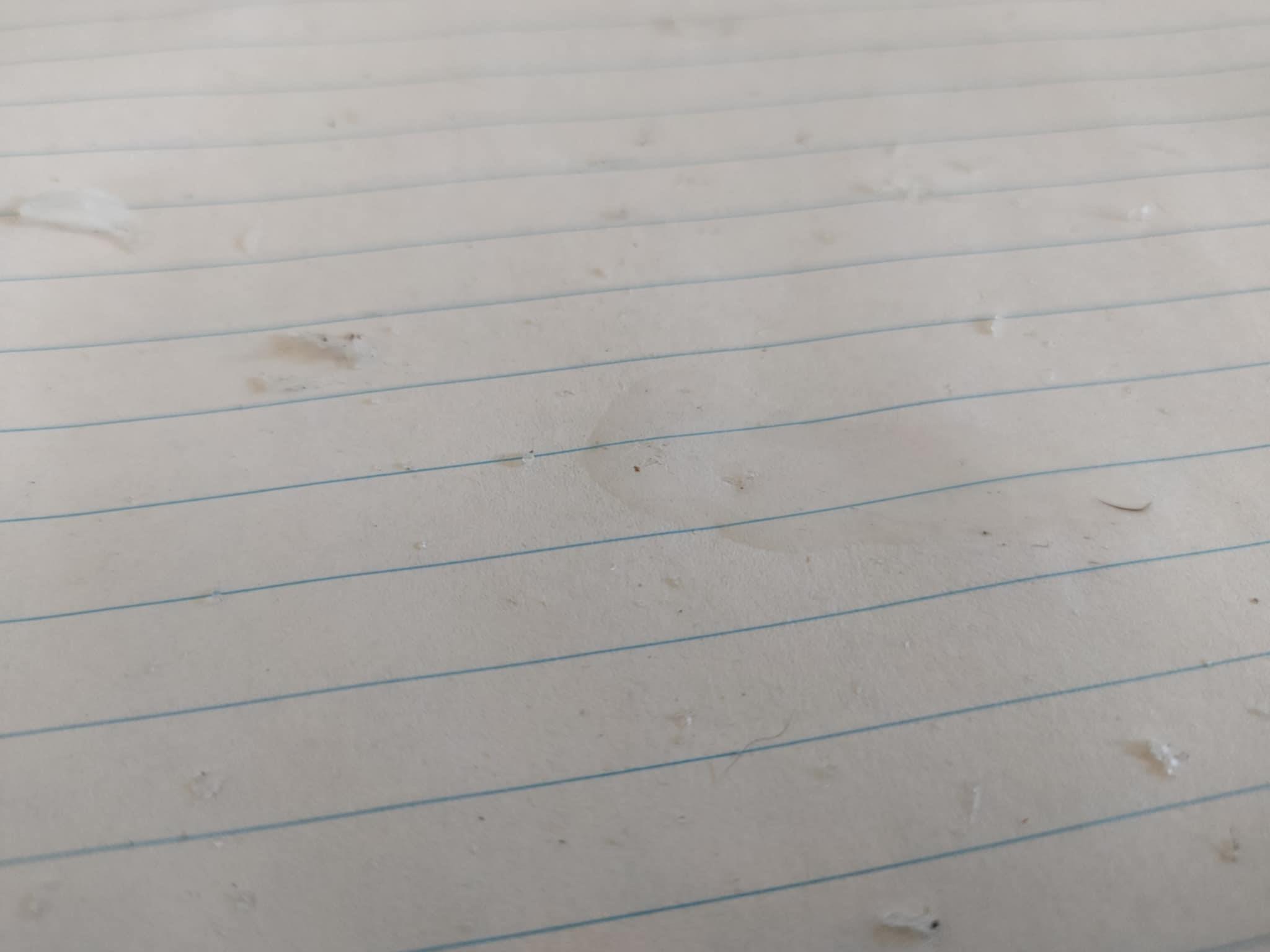
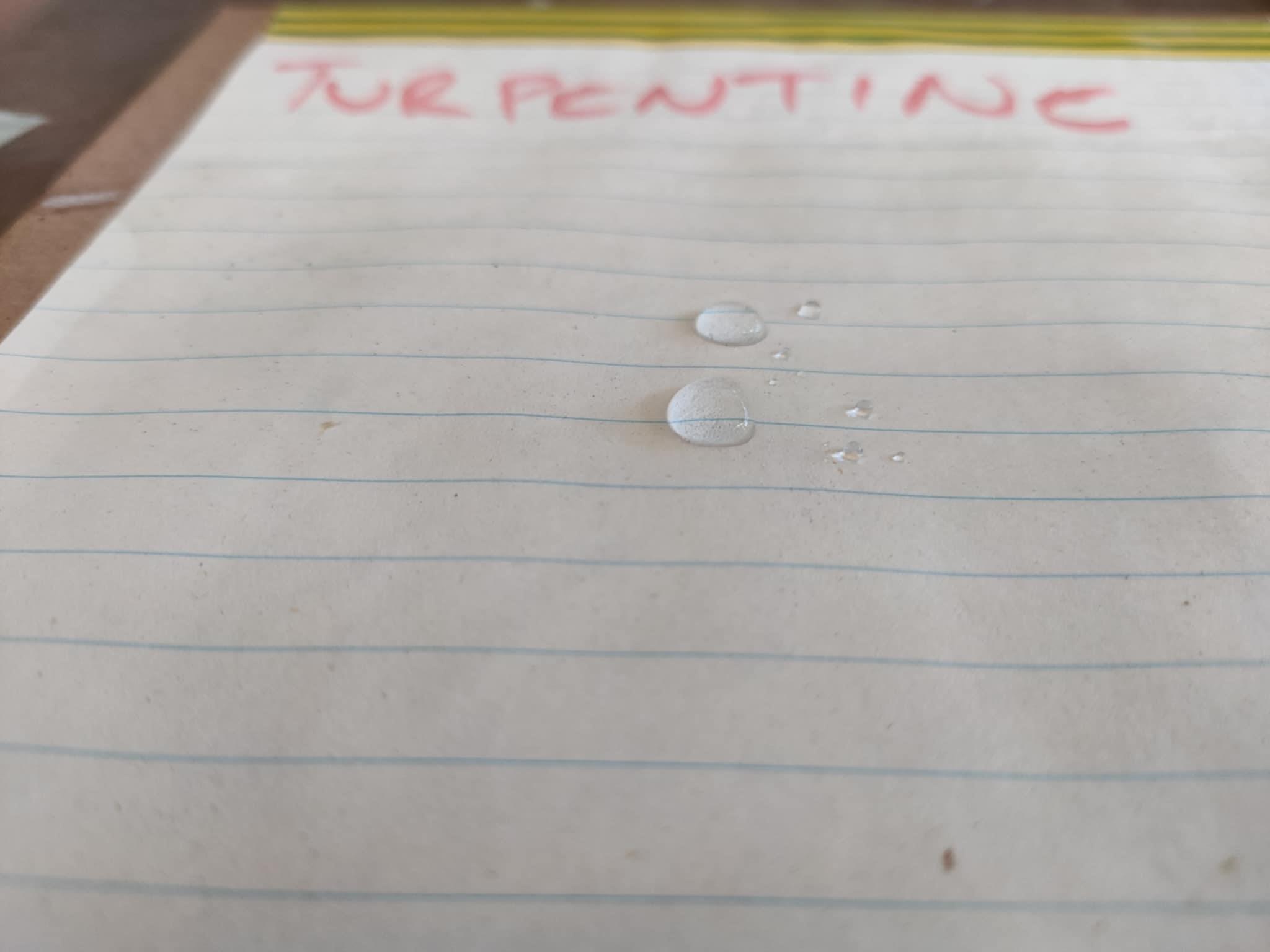
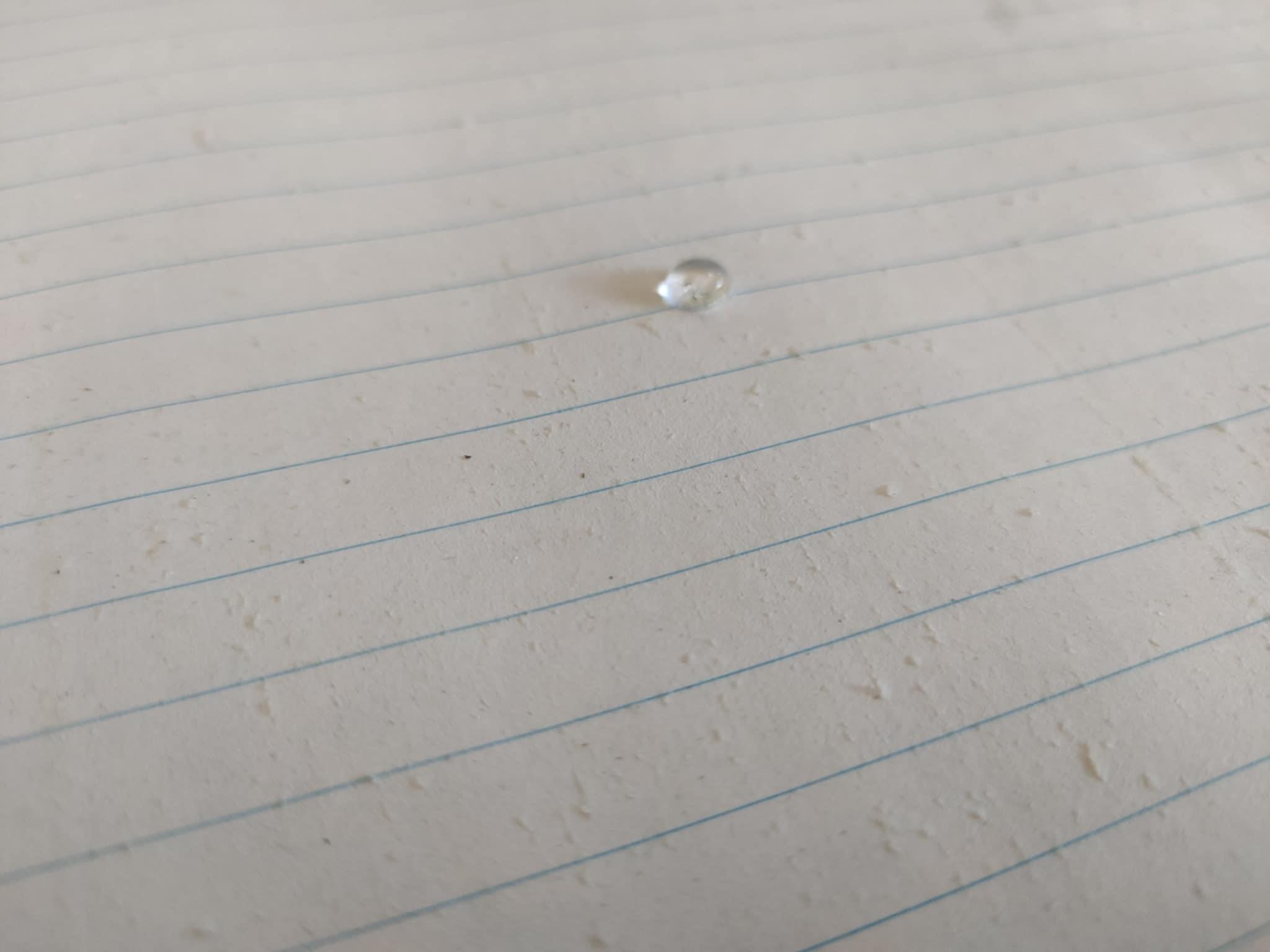
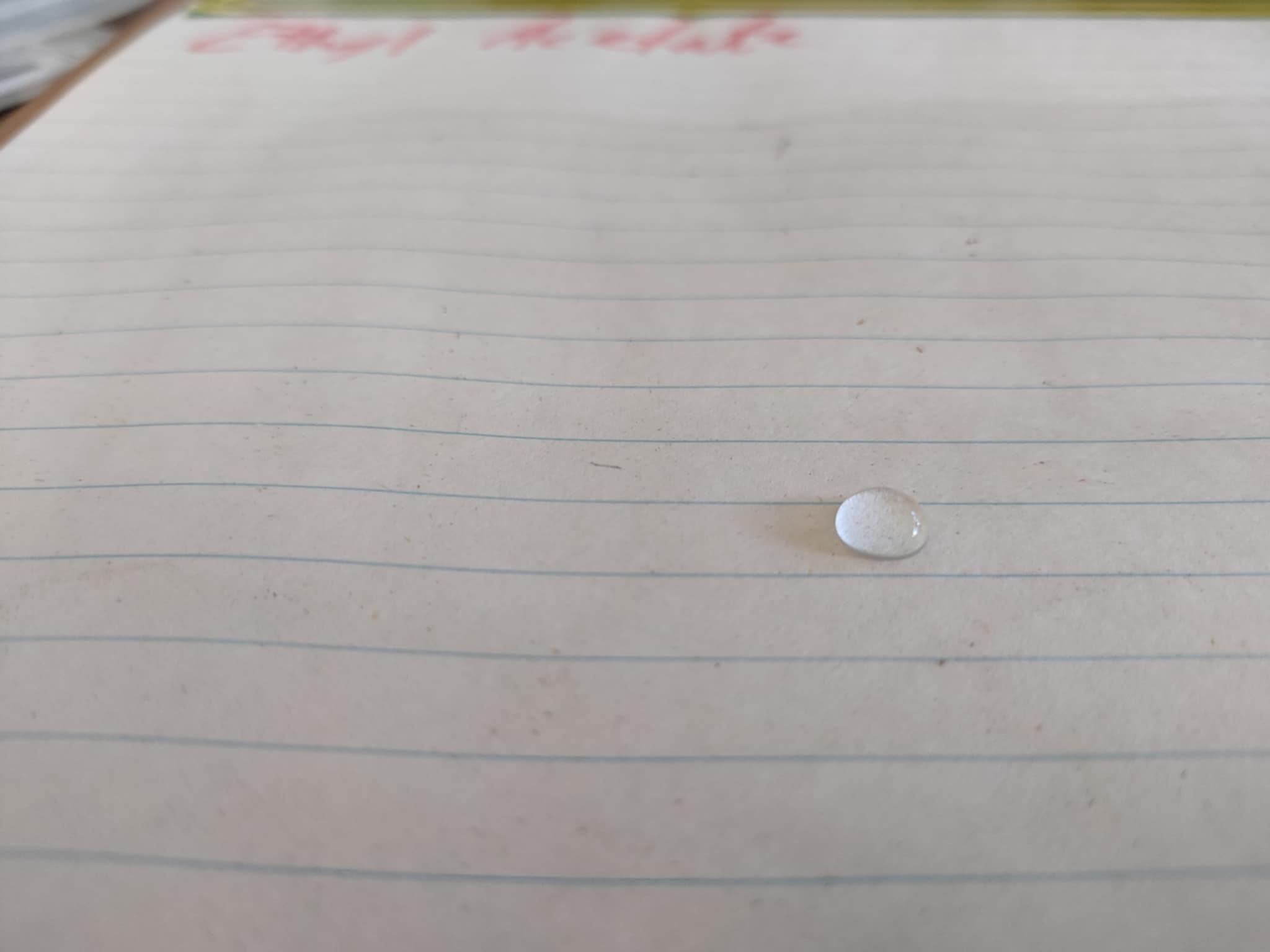
.jpg)
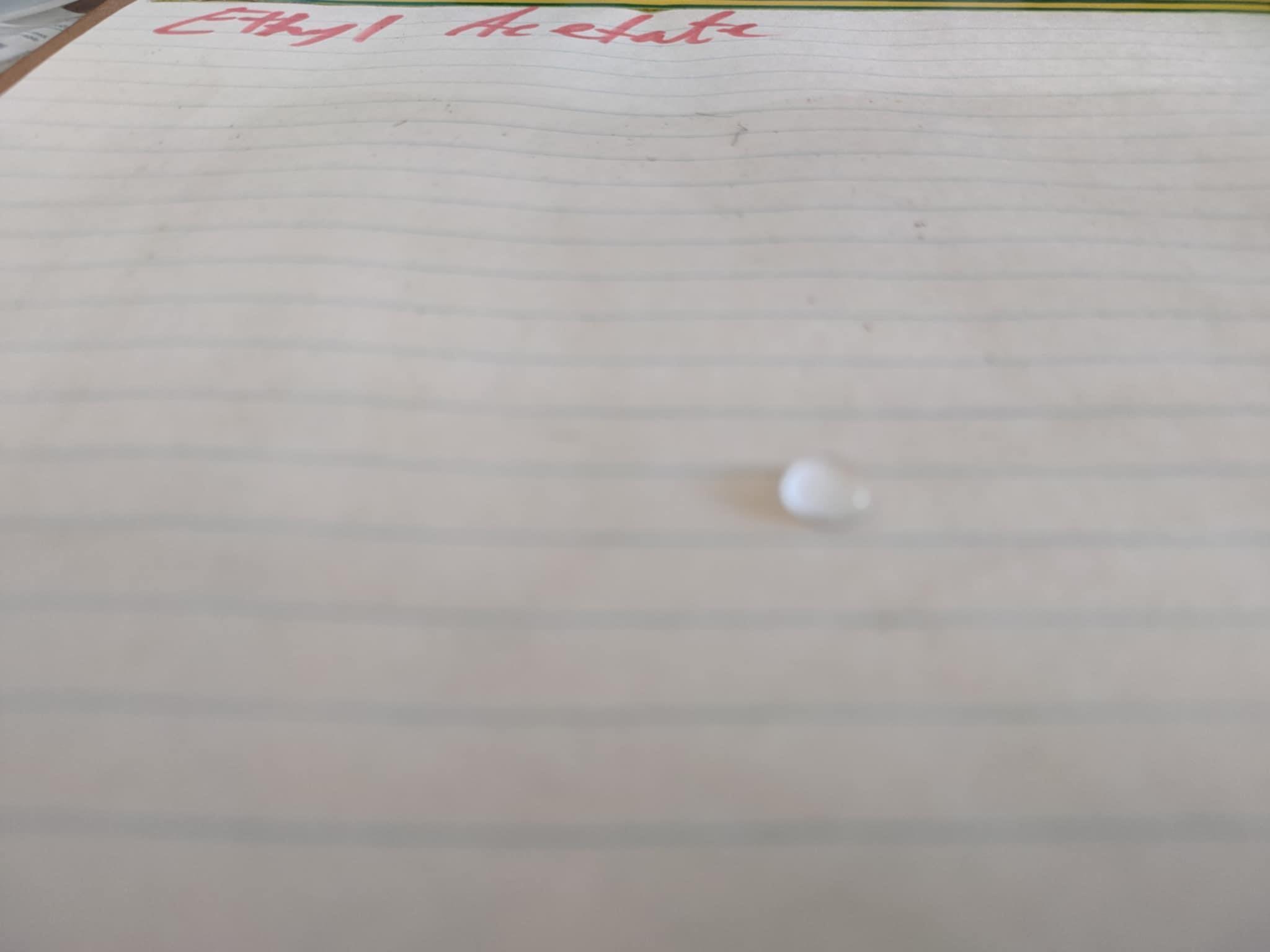
This test was reasonably straight forward, did the layer repel water enough to protect the underlying paper (which is absorbent to water, in most cases). Each surface had a fat drop of water deposited, and I checked to see if the water would bead and run around on the surface (water repellant) or if it would be absorbed or smear (water absorbent). Essentially we're visually confirming the hydrophobicity of the surface coating has been achieved.
As you can see in the images, all bar one of the samples exhibited excellent hydrophobicity, or waterproofing). The outlier was the methylated spirits sample, on which the water spread into a large dispersed droplet, with a low contact angle. This indicates that the mix didn't apply a strong hydrophobic layer, and the water is able to permeate into the papers fibres.
Is It Resistant to Marking?




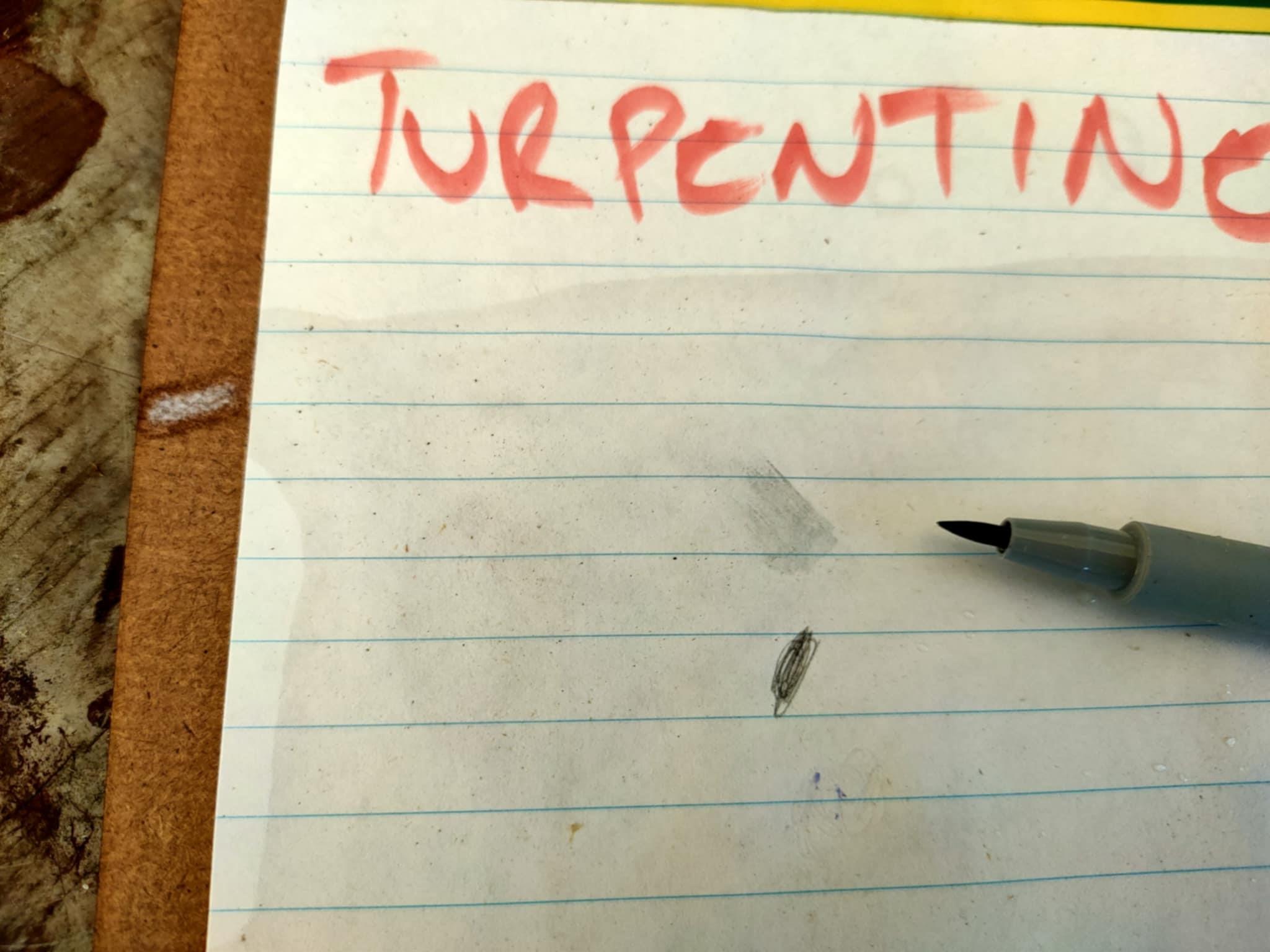
Now if the intent is to use this mixture in future projects, I would need to know how it will behave with response to colour. We can see that the silicone layer is relatively clear, so any marking or printing on the paper prior to waterproofing should be visible afterwards, but can the paper be marked after the fact?
This test was performed on the Turpentine mix sample only, but I am confident that all 5 of the well coated samples should behave similarly.
My initial expectation was that the white-board (dry-erase) marker I was using with the paper in this project would write on the surface, then be wiped away afterwards. I was very surprised to find the erasable marker actually permanently marked the coated paper!
This convinced me to try other types of stationery. The biro (a water-based ink) wasn't able to mark the page, but graphite pencil lead did. My final test was with a felt-tip pen, which was able to deposit ink on the page but it didn't adhere, and was able to be wiped away/smudged with a finger.
So the coated paper can be written on, provided you're using a solvent-based marker or pencil, but not a biro. If you wanted any custom prints or patterns on the paper, I'd probably print them on the paper first and coat it later.
Mechanical Testing




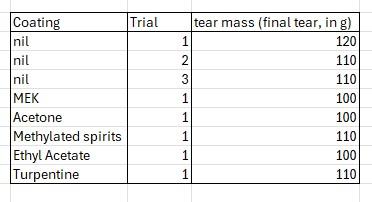
Now in addition to being lightweight, foldable, and waterproof, Tyvek is also quite tear resistant. I wanted to determine whether my coating improved the mechanical properties of the paper (ideally shear resistance, or resistance to tearing).
To test this I built a small jig, wherein sections of the samples were cut to a template designed to promote tearing along one axis (see the image). Essentially strips were cut 20mm wide, with a slit in the middle. One side of the slit was taped to the tabletop, and weights suspended by a clamp from the other side. My theory was that increasing masses until the sample tore along the pre-defined line would give us an estimate of any shear-resistance the coating had made.
3 "nil" samples were cut from non-coated paper of the same type, to get a baseline to compare our mechanical testing results against. The results were tabulated in the attached image.
The results for our coated samples were... not great. There was no extra resistance to shear imparted by coating the samples with the silicone mixture. If anything, treating the surface seemed to slightly decrease the shear resistance.
So... strengthening the paper with the coating is a bust. The smooth surface might give it a little resistance to wear, but I don't think I'll be using paper in the future for its abrasion resistance, anyway.
Water, Yes, But What About Fire...?

This last one was an unprompted test. Does the silicone layer provide any resistance to heat? My test setup for this was quite simple, using a handheld jet style lighter (high focused heat) and a ruler held perpendicularly to the papers surface, how far from the surface does the lighter need to be to begin scorching?
This was especially difficult to photograph during testing, so please see the mockup I photographed after the test.
From a few quick samples, this lighter could scorch untreated sheets of paper from approx. 55mm away from the surface. Treated side up, this number shrank to about 40-45mm (varied over testing). This shows that the silicone layer does give some thermal resistance, although not enough to claim to make it fire resistant.
Results!


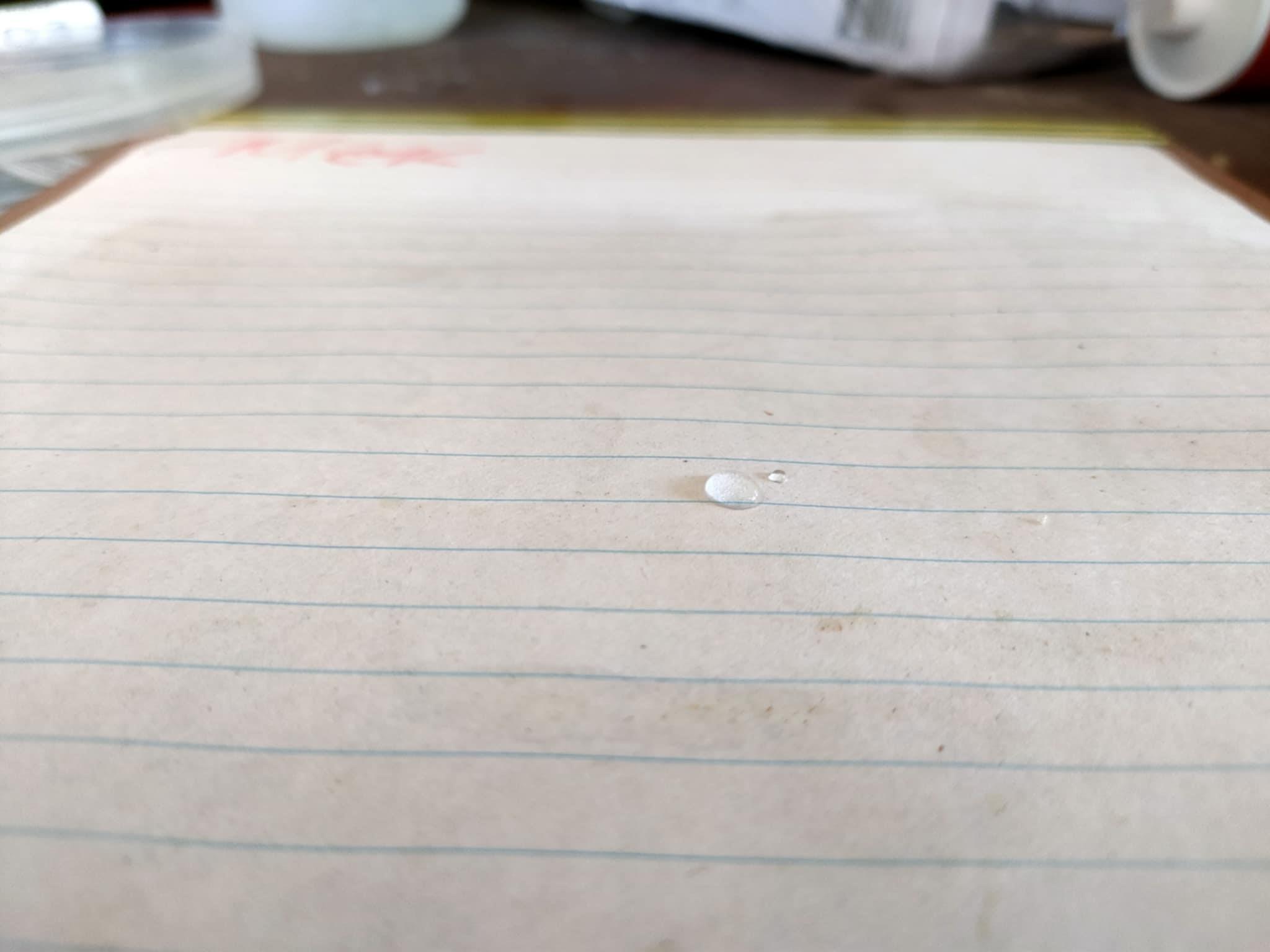
So we trailed 6 solvent/silicone mixes, to see if we could treat paper for water and mechanical resistance (and fire!). Of the 6 solvents, methylated spirits (aka ethanol) was the clear loser, poorly mixing with the untreated silicone and not forming a stable layer on the treated paper. I am not entirely sure the silicone didn't partially cure while immersed in the solvent before applying it tothe paper. This left a water permeable surface with large chunks of silicone caulk stuck to the surface.
Acetone was the next worst performer, because although it did form a water proof layer, there was still lots of small balls of silicone distributed across the surface, rather than a smooth consistent layer.
Of the other four solvents, all of them made a smooth waterproof layer on the paper, but of the 4 I would suggest ethylene acetate (followed closely by shellite) to be the best performers, leaving even layers of waterproofing on the paper surface with minimum discolouration. Of the two, shellite is much cheaper, so unless surface colour is absolutely important I would probably use this as my solvent going forward for other projects.
All of the samples were tested for improvement in shear resistance, but had no demonstrated improvement.
An example of the silicone coated samples was tested for ink/dye penetration (ie written on with various implements) and as suspected water based pens had difficulty writing on the surface, but graphite and solvent based markers could still permanently mark the paper.
While the coating did provide *some* resistance to scorching, it wasn't appreciable.
What's Next?

So the quest for homemade Tyvek continues. In the meantime, I have a recipe (6 parts shellite to 1 part silicone) to coat paper samples to make them waterproof but still susceptible to marking from pencils and some markers. Not enough to apply for a patent on, but some good knowledge for future projects, or further research down the line.
In the meantime, I've taken the remaining sections from my samples and made a little pocketbook to carry around for notes, with a pencil tied on with a string. Now I have a little waterproof way to take notes on the fly. Waste not, want not.